真空チャンバーの覗き窓がポリエステル樹脂で白濁してしまいました!
Amazonなどで販売されている真空チャンバーのフタはアクリル板のモノも多かったので、よく考えずポリカーボネイト板を使用していました。
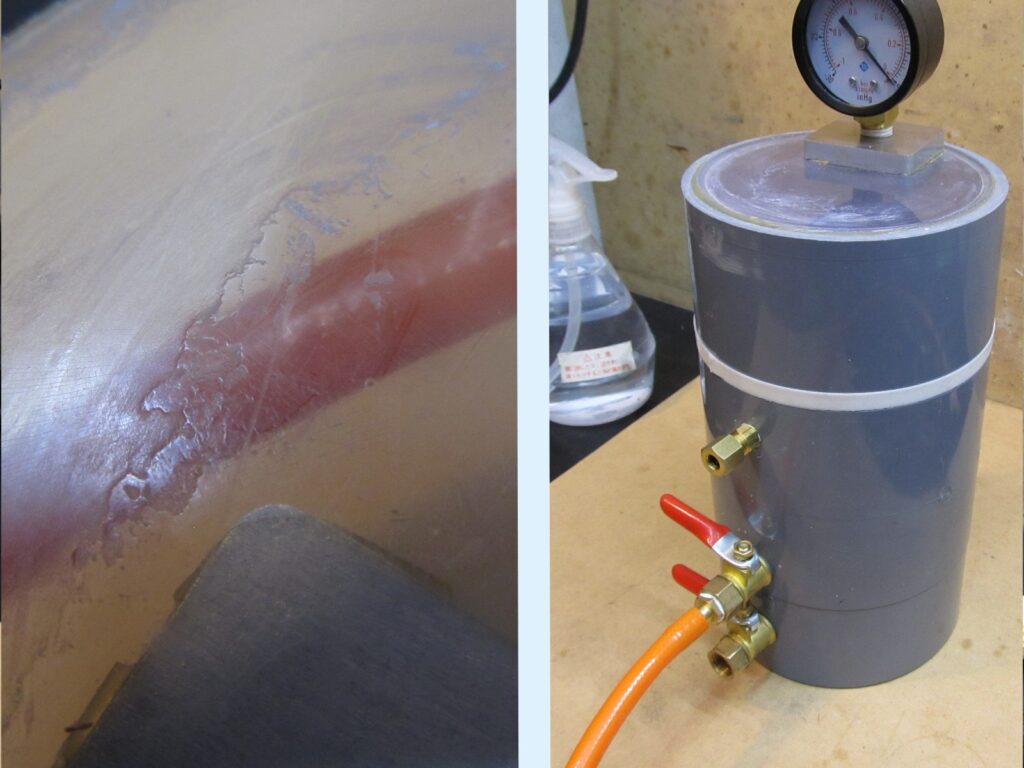
材質はよく勉強した方がよさそうですね。
ポリカーボネイトは溶けます
白濁した窓はポリカーボネート板6㎜厚。
ポリカーボネイトは耐衝撃性がバツグンなので真空圧がかかるチャンバーにはもってこいかと思っていました。
ところが、前回のインフュージョン実験で真空チャンバー内にポリエステル樹脂が複数回霧吹きのように噴き出し、ポリカーボネイト板に付着し放っておいたところこのように白濁色に・・・。
ペットボトルやプリンのカップなどと同じように「ポリカーボネイト板も同じように付着してもパリパリと剥がれるんじゃないか・・・」と勝手に思い込み放置したのがまずかったですね。
アクリル板もやめた方がよさそう
以前この真空チャンバーの窓は同じ6㎜厚のアクリル板でしたが、何度か使用しているうちに真空圧に負けて割れました。
アクリル板は、新品時には真空圧による変形はほとんどなく6㎜厚で十分そうでした。
急にもろくなって割れたような印象があります。
もしかしたら、これまで中に引き込んだ有機溶剤、樹脂などの蒸気でアクリル板がもろくなっていたのかもしれません。
真空チャンバーには様々な合成樹脂や溶剤を引き込むことになるため、「樹脂製」覗き窓はやめた方がよさそうです。
「耐油性、耐薬品性、耐溶剤性」を考えると身近な材料で無難なのは・・・「ガラス」と思われます。
ガラス板の加工
円形ガラス切りを購入して自分で加工!に挑戦しました。
厚さ10㎜のフロートガラスを購入。 直径113㎜に加工します。
ネットで一番安かった「株式会社 コーワさん」から購入です。
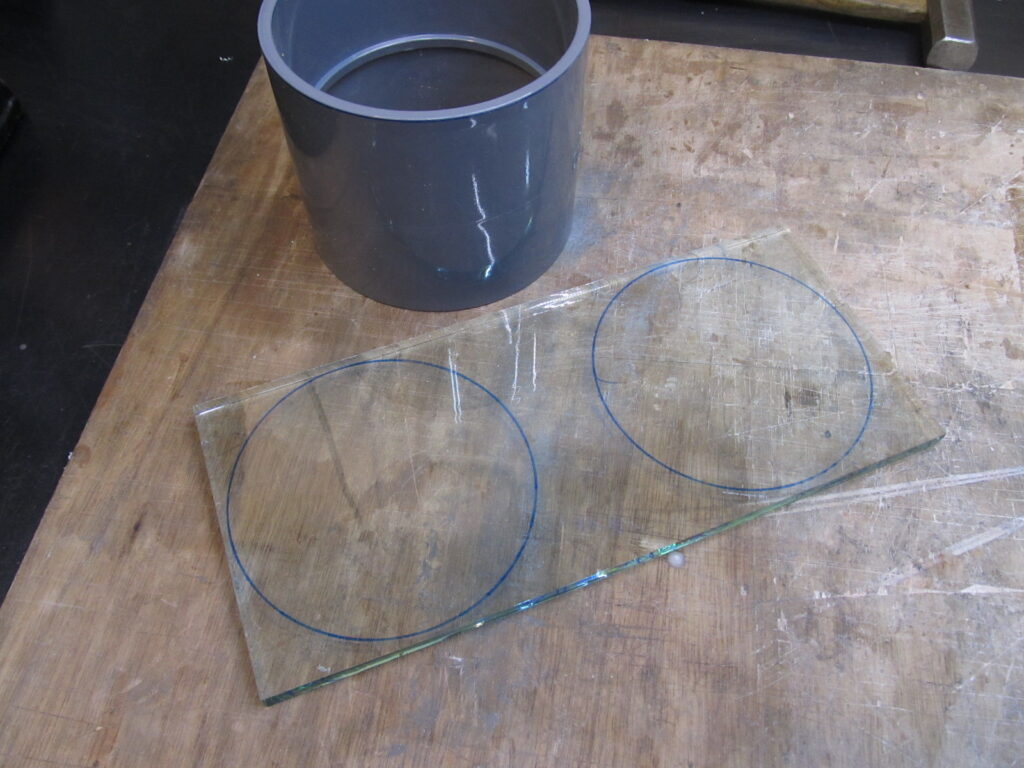
結果、高くても加工を頼んだ方がよかったな・・・。
ガラスの切り方をネットの動画で参照しましたが、動画のようには上手くいきません。
直線カットなら動画のようにパリンと割れますが、10㎜厚の円形カットは素人には厳しい。
ガラス切りでキズを入れた後、コツコツ叩いてプライヤーで挟んでも人力では割れる気配もありません。
変な割れ方をしてガラスを無駄にしたくないので確実に割れるようダイヤモンドホイール+リューターで加工することに。
【写真】水をかけながら深めの溝を入れてニッパーで割っていきました。
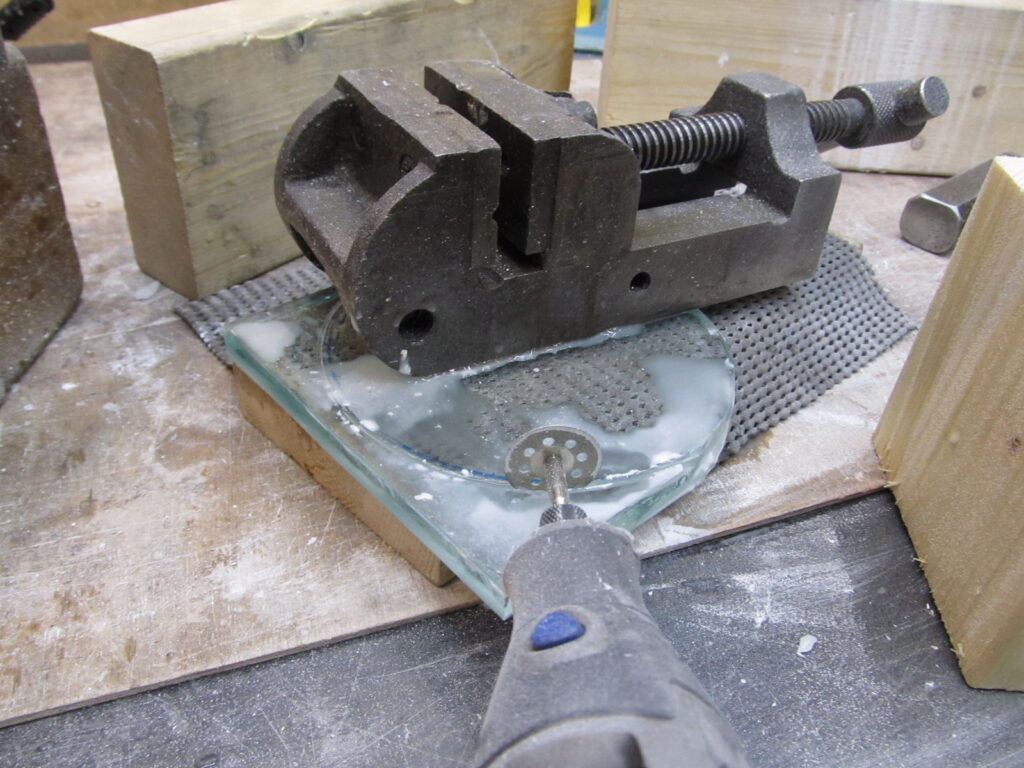
【写真】凸凹の外周をダイヤモンドディスクで整えます。
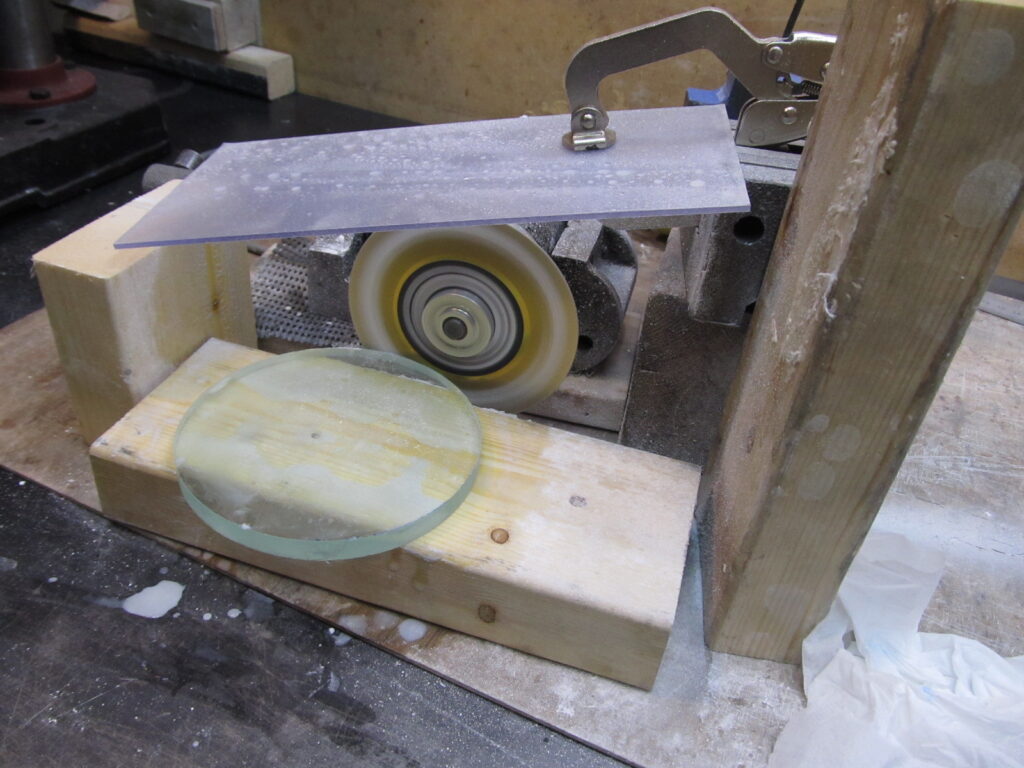
【写真】真空ゲージ用空気穴を開けます。

【写真】加工に2時間以上かかってしまいました。
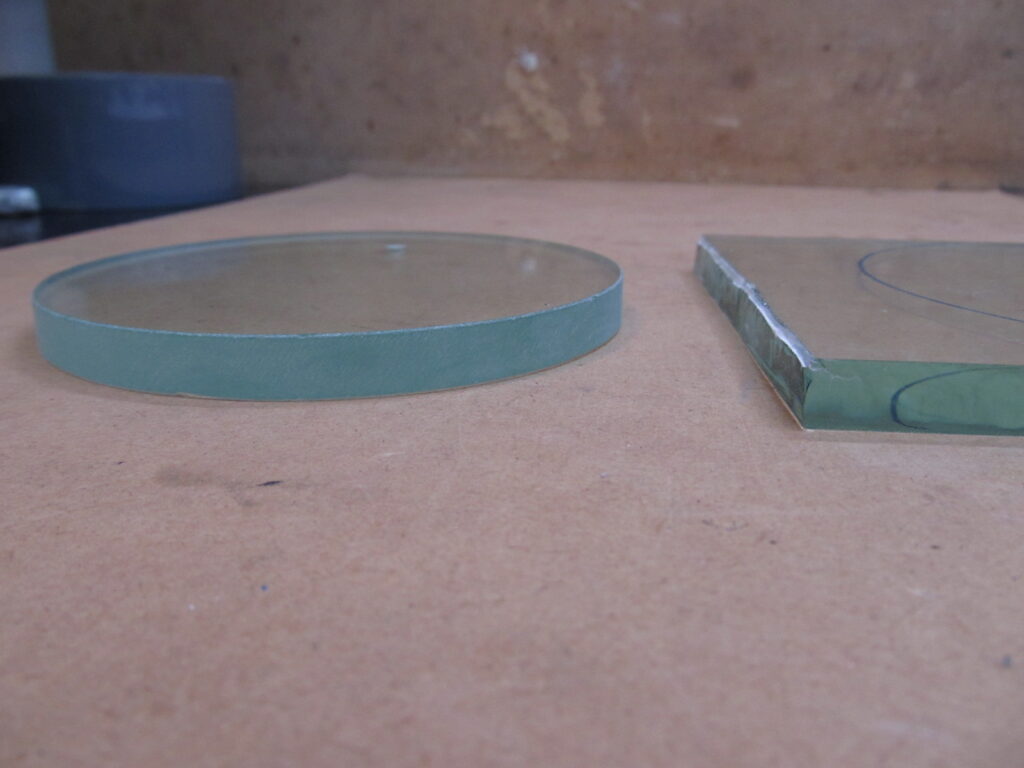
強化ガラスではありませんが、「10㎜もあれば真空圧に負けることはないはず!」とあてにならない勘が言っています。
強化ガラスはカットできません
↓ ↓知らないで購入した強化ガラスを直線カットした図
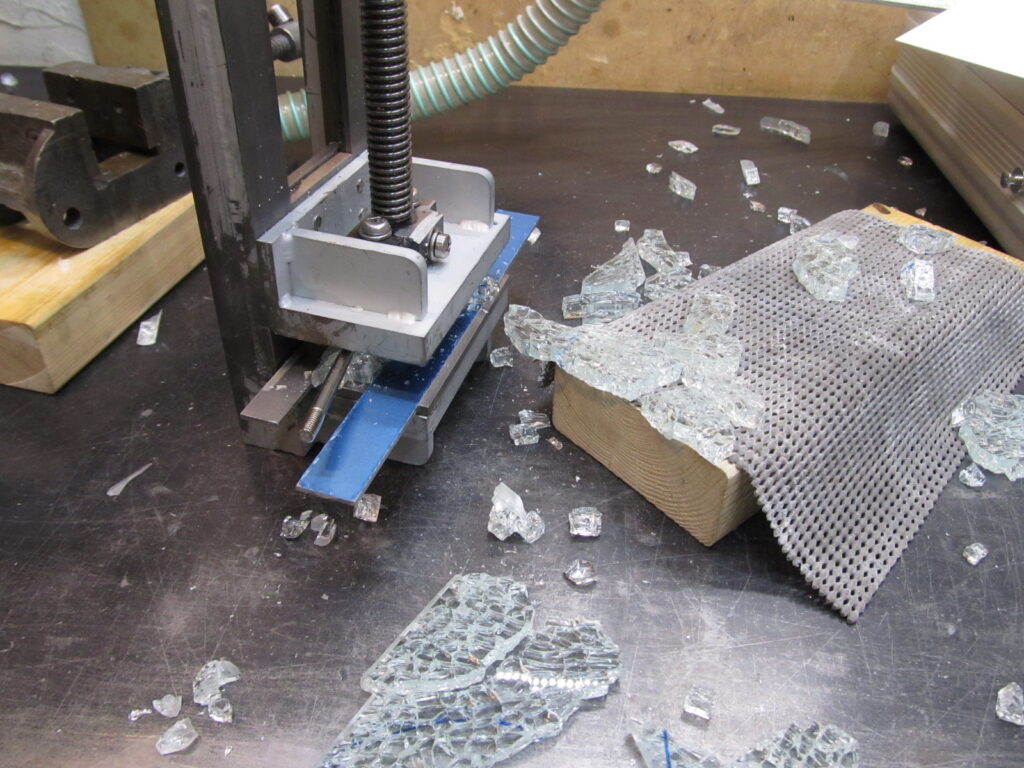
強化ガラスは熱処理でガラス表面にテンションがかかっているらしく、ガラス切でキズをつけ割ろうとすると一気にテンションが崩れて「ボンっ」と割れます。
ビックリしたー!
ガラス板に交換完了
2時間かけてカットしました円ガラスをポリカーボネイト板と交換して修理完了です。
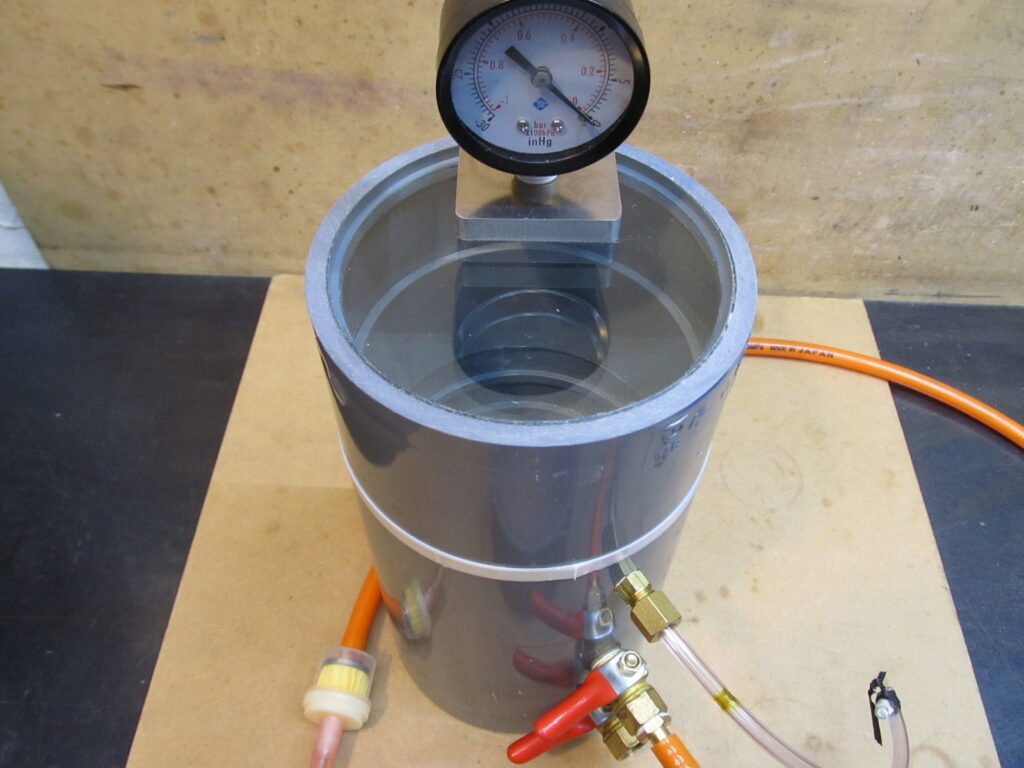
ガラスだと樹脂板よりキズに強いし溶剤に侵される心配も少なく安心です。
心配なのは真空圧にどれだけ耐えれるかです。
円形加工時に「ガラスってかなり強度があるなあ」という感触を得ましたので、おそらくこんな小さな直径のチャンバーなら大丈夫でしょう。
さて、覗き窓をガラス版に交換出来ましたのでこの勢いで余ったガラス板を使ってもう一台真空チャンバーを作製しておきます。
予備です予備!