ゲルコートの縮れから作成作業が中断してしまいした。
悔しくてどうしても「カーボンFRP製品を確実に成型する」自分なりの工法を確立したくなり実験にハマってしまいました。
ある程度分かってきたので・・・・
カーボンFRPを自作してみたいという方の参考に!と実験から学んだことを記事にしておきます。
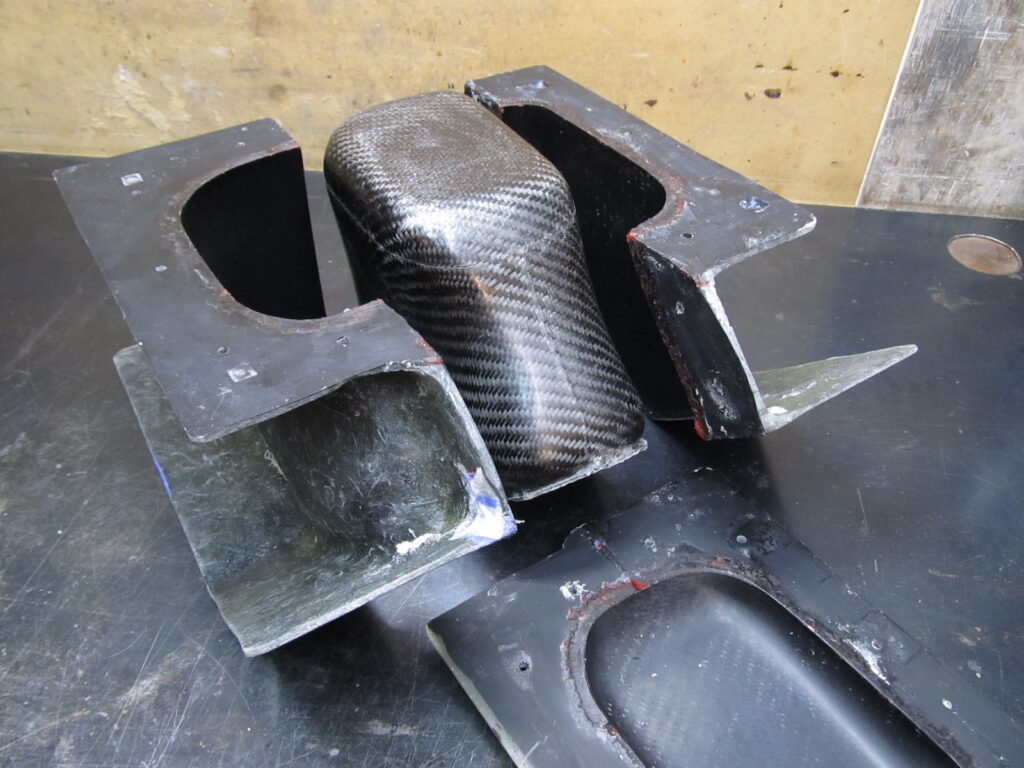
初めにお伝えしたいのは「カーボンFRP自作を楽しむために、手間もお金も惜しんではならない!」です。
FRP工作って面倒なので「適当に作業しちゃおう・・・ 高いから安価モノで代用しよう・・・」となりがちですが、横着すると大抵失敗して時間とお金とやる気を失います。
というわけで、余計な回り道をせずやる気を失わずFRP工作を楽しむために失敗から学んだことを記録していきます。
(この記事は原型⇒雌型⇒インフュージョン成型という、ちょっとガンバって美しいカーボンFRP製品を作製することを前提にしています。)
動画にもまとめてみました。読むより早いかも。↓↓
目次
原型の芯の作製
「原型は、発泡ウレタン+ガラスマット+ガラスクロス+ゲルコートで作成する」が基本です。
紙粘土やら、石膏、石粉粘土、スタイロフォーム・・などホームセンターや100均で入手できる材料を色々使ってきました。
簡単に確実に満足のいく原型を作るには、多少高価でも「発泡ウレタン+ガラスマット+ガラスクロス+ゲルコート」を使うのが一番の近道だという結論に達しました。
発泡ウレタンを使った原型作りの詳しい説明はググるとたくさん見つかりますので基本的なところは割愛し、azarashi工場長が気を付けたい!と思ったポイントを挙げます。
発泡ウレタンは2液混合型、30倍発泡 を使う
購入時期によりますが1kg(0.5Kg+0.5Kg)で3000円弱と少々高価です。
でも、使ってみるとそれ以上の価値アリと思うハズです。
〇2液混合型の理由
安価で簡易な発泡ウレタンといえば1液型のスプレー缶入り(おもに建築用)。
この1液型発泡ウレタンは空気中の水分に触れて硬化するので内部まで硬化するのに1日以上かかってしまいます。また、ボコボコに不均一に発泡するので切削し形を整えるのにひと苦労します。
2液型は少々高価ですが、硬化の速さ(1時間程度で内部まで確実に硬化)、均一に発泡する、というメリットを考えるとお値段以上の価値はあります。
〇30倍発泡の理由
計算どおりに30倍になることはなく大抵少なく発泡しますので体積を稼ぐため発泡率は大きいモノを選択します。
30倍だからといってスカスカになるんではとの心配は無用です。 サクサク研磨できて原型作製にもってこいの硬さです。
1Kgで3000円近く、と湯水のように使える材料ではありませんが、サクサク研磨できて平面出しも容易な素材は他になかなかありません。
発泡ウレタンを使用すれば原型のコア(芯)部分を少ない労力で短時間で仕上げられます。
原型の表面仕上げ
「ガラスマット2層+ガラスクロス1層+ゲルコート(インパラ)で仕上げる」が基本です。
発泡ウレタンはポリエステル樹脂に溶けないので直にFRP積層ができます。 ホームセンターのスタイロフォーム(青い発泡スチロールのようなモノ)は溶けちゃいます。
ガラスクロスを必ず使い、ガラスマット⇒ガラスクロスまで連続的に積層する
ガラスマットのままで硬化させると表面がかなりでこぼこになります。ハンドレイアップで積層しますが、刷毛などでガンバって平滑な面が出たなあなんて思っても硬化後は結構デコボコ凸凹。
凸凹といっても1㎜程度ですが、カチカチのポリエステル樹脂の面を研磨で1㎜下げるってかなりの労力ですよ。
ガラスマットの凸凹面を手作業で平滑にすると思うとテンションが下がってしまいます。
そのためガラスマットが硬化する前にガラスクロスをすぐ積層し硬化前(樹脂が液体のうち)に平滑にしておきます。
これで硬化後の研磨作業が各段に楽になります。
「ガラスクロスまで一気に貼る」ここでのひと手間が後の「楽々」につながります!
ゲルコートはスプレーガンで均一に吹く
原型のゲルコート(インパラ)は必ずスプレーガンで吹きます。(雌型のゲルコートは刷毛でもOK)
先の理由と同じく、硬化前に平滑にすることで切削・研磨作業の軽減を図ります。
刷毛の凸凹でも耐水ペーパーで切削、研磨で均すのってかなりの労力。
なかなか平滑にならないなあ・・・と長時間研磨しているとR部分や角が思った以上に研磨されゲルコート下のFRP層が出てしまいます。こうなるとまたゲルコート積層やり直しです。
こんな苦労はスプレーガンで吹くことで一掃できます。 スプレーガンは清掃が手間ですが研磨の苦労と比較すればなんてことありません!
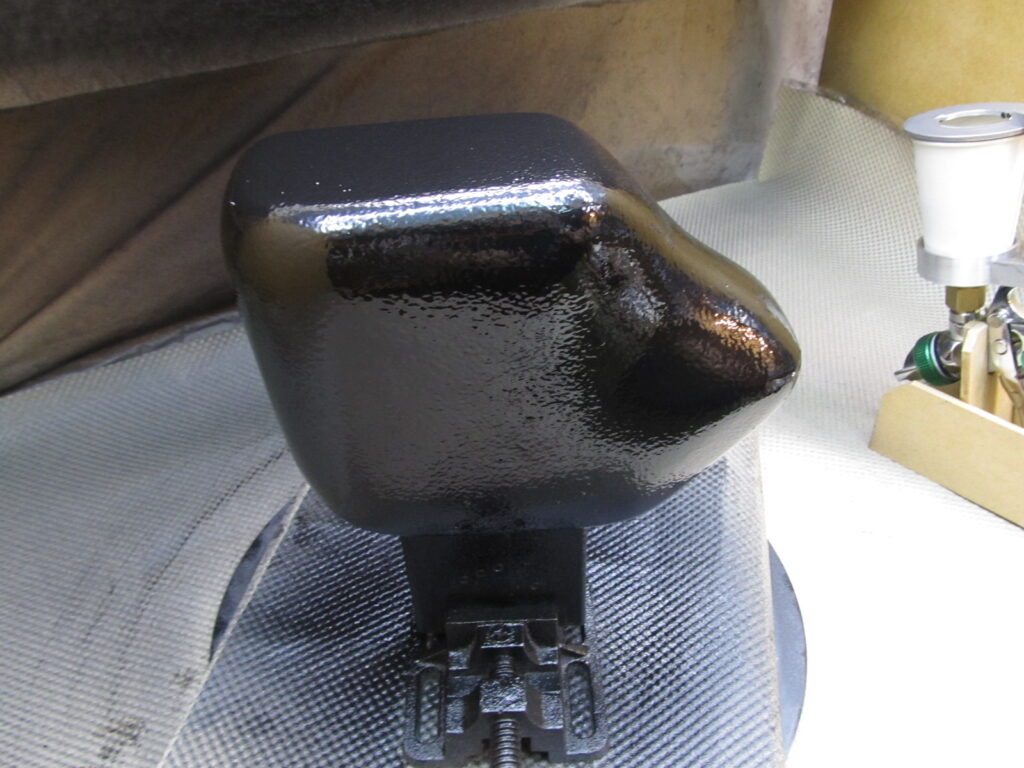
ゲルコートをスプレーガンで吹くと梨肌というのでしょうか、波打った凸凹になります。
この凹んでる部分を目標に(凹みがなくなるように)研磨すれば下地のFRPが出てくることなく黒い平滑な面を得られます。
研磨しすぎず平滑面が出せるのは心の平安です(笑)!
※重要:ゲルコートは必ずインパラで!
ノンパラだと表面が未硬化でベトついたままになります。 このベトつきが研磨作業の多大なる妨げになります。
雌型の作成
ゲルコート+ガラスクロス3層が基本です。
分割式にすることをためらわない
複雑な形状、向かい合う平面があるなど、雌型を分割式にした方がよさそうだと思ったらためらわず2分割、3分割にします。
分割式は作成が面倒ですが、これくらいなら何とか離型できるかなと横着すると、雌型と硬化した製品が噛み合ってしまい2度と外れなくなります。 これまでの作業が水の泡に・・・。
こんなイメージで分割型を作ります。
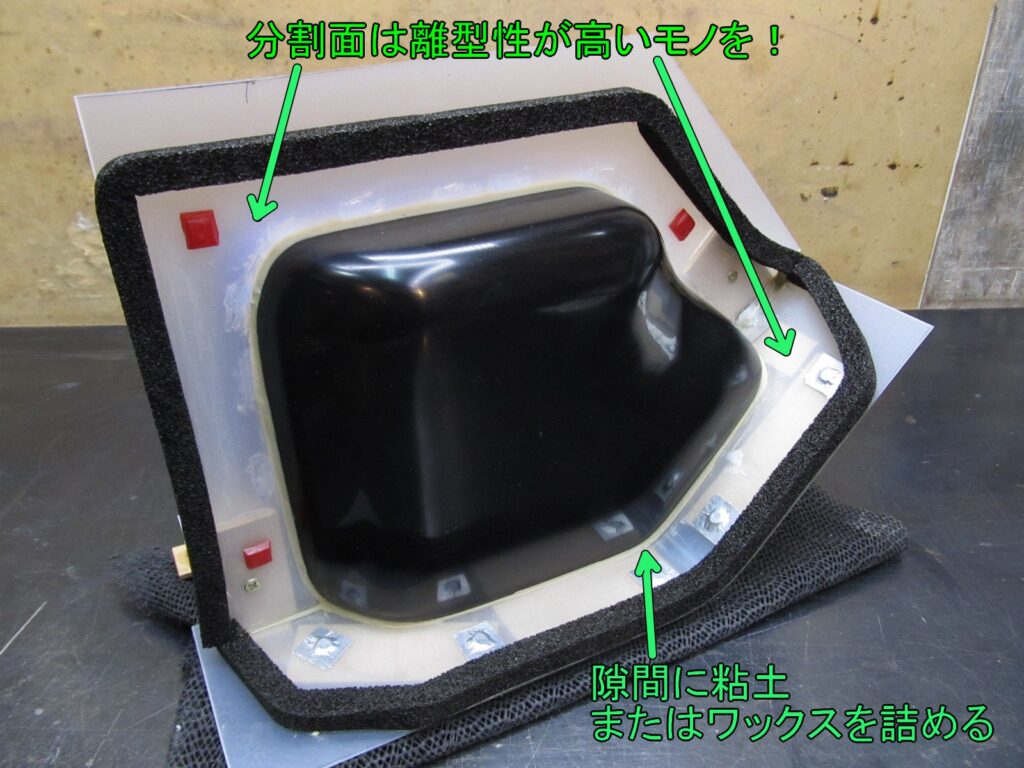
この分割面を作るのが結構な手間。
この手間を省く案はないものかと日々苦悩しておりますが、今のところ避けがたい工程。 我慢して作るしかありません。
※重要:分割面は少ない力で離型する材料を使います。
ポリプロピレン板またはMDFボードに100均のアルミテープ貼りがおススメ。
雌型を2回に分けて積層しますので、途中、原型と雌型(初めの片側)が外れないように分割面だけを取り除くステップがあります。
その際、こじらずにペリっと外れる分割面でないと原型と雌型(初めの片側)が外れてしまうことがあるので要注意。
途中で外す分割面が簡単に外れるための事前準備が一つの難関ですね。
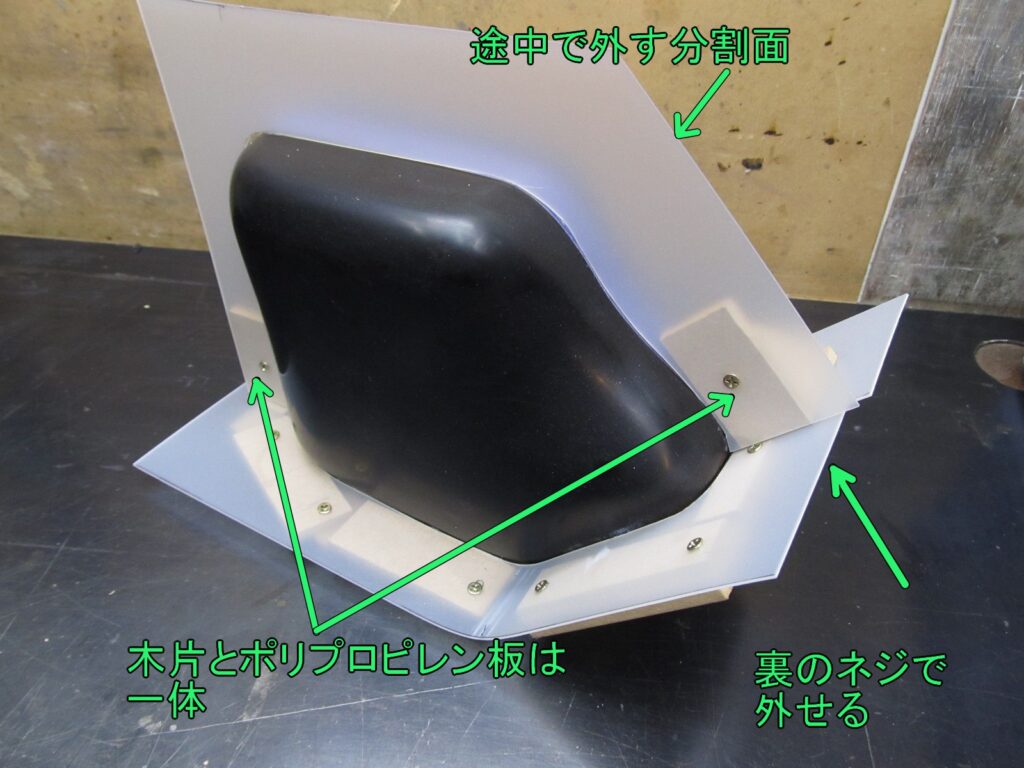
参考にした海外のyoutube動画ではスマートにサクサクと分割型を作っておりますが、実際やってみると結構大変な工作です。
図画工作が苦手・・という方は「もう、やーめたっ」となりそうです。(笑)
FRP工作は型作りが8割!と言い聞かせてガンバリマス。
離型剤はワックス+PVAを使う
確実な離型を期するためPVAは必ず使用します。
詳細は「FRP離型の実験 洗濯糊代用のPVA離型剤」を参照。
PVA離型剤は市販のモノでも自作の洗濯糊代用のモノでもOKです。
離型処理は、2つ前の写真の状態まで分割面の設置が済んでから行います。
ゲルコートは刷毛塗りでもOK
雌型の場合、刷毛で塗りで凸凹していても次に来るのはガラスマットの積層。凸凹は問題ありません。
ただし、ゲルコートはノンパラを使用します。

写真ではスプレーガンで吹いていますが、刷毛で塗ることの方が多いです。
ガラスマットは事前に型取りしてカットしておく
ガラスマットは手でちぎれるのでちぎりながら積層していく方も多いようです。
コーナーなどほぐさないとフィットしない箇所はちぎりながら積層しますが、出来るだけ事前に原型に合わせてカットしておいた方がスピーディに作業が進み樹脂の硬化時間が気になりません。

原型に面する部分はガラスマット#450を3層程度でOK。
フランジ部分と原型とフランジの境目(直角になる部分)は5層、6層と分厚くして本番の離型時に力をかけても割れないようにしておきます。
分割面を丁寧に取り除き反対側も積層
分割面をそ~っと取り除いた後、同じ作業を繰り返します。
分割後の面の粘土やワックスを除去、再度隙間に粘土を詰める、PVAで離型処理するという流れです。
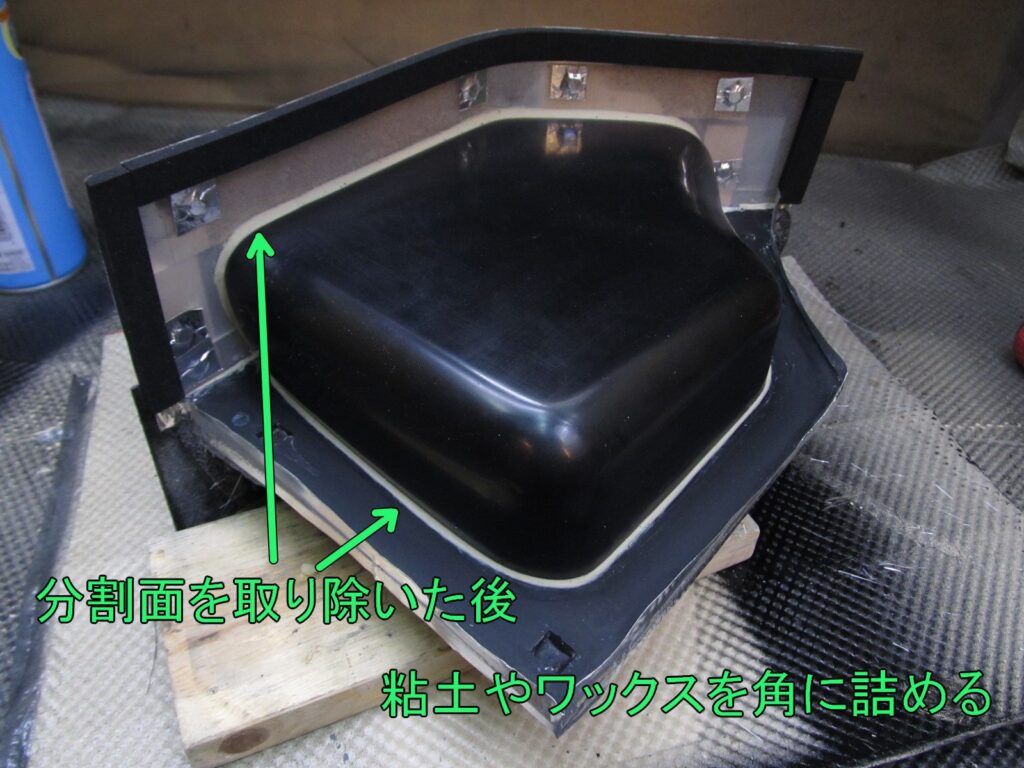
原型と雌型の分離
ガラスマットのみで積層しているので表面がバリバリです。 ケガに注意!
なんとも美しくないFRPに原型がくるまれており、外れるのだろうか?と心配になります。
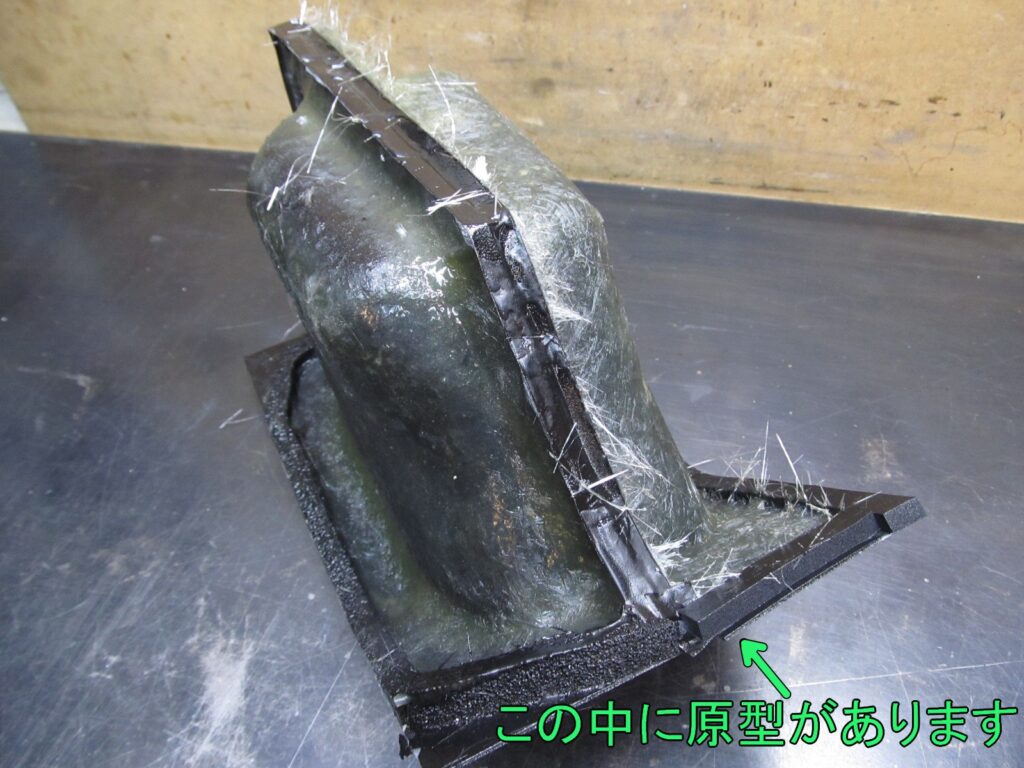
初めにケガ防止のため80番程度の粗い布ヤスリでバリを落とします。
次に外周をグラインダーでカットしていきます。 そうすると左右の分割ラインが見えてきます。
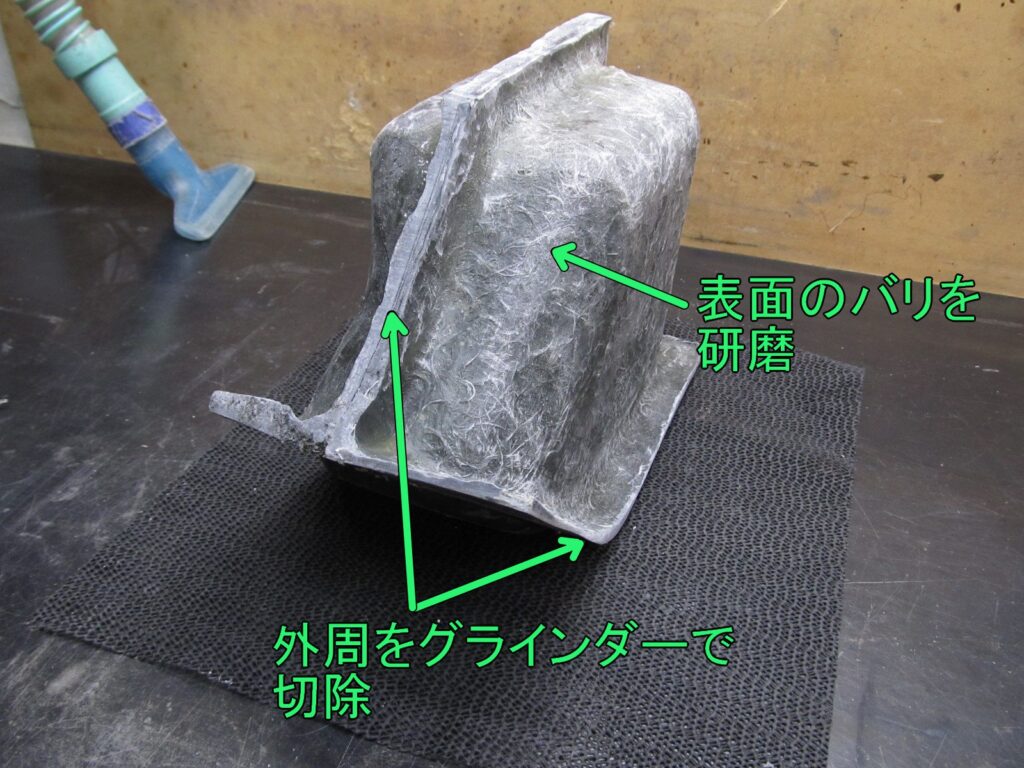
分割ラインにカッターナイフを差し込む⇒薄いマイナスドライバーを差し込む⇒太いマイナスドライバーを差し込む・・・と順を追って厚いモノをクサビのように丁寧に打ち込んでいくと、パンッと外れます。
PVAを塗布している場合、本当に簡単にパンって外れます。 嬉しい瞬間です。(笑)
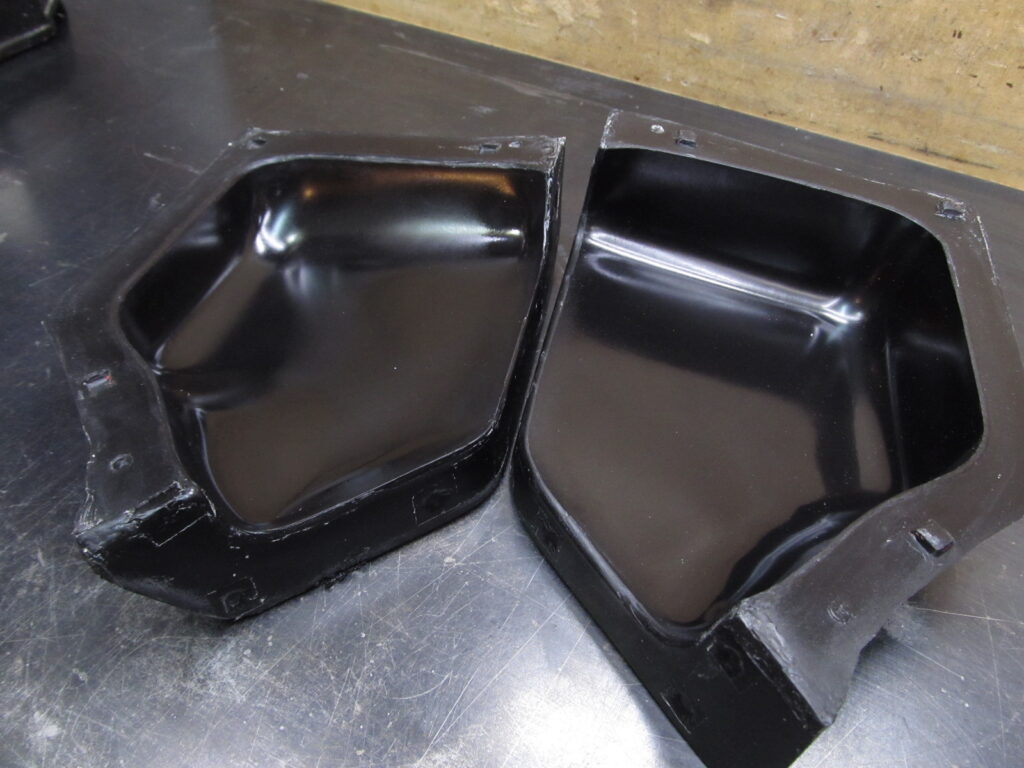
型にPVAの膜が残りますので、水道で洗い流せばピカピカになります。
これでカーボンパーツを何度でも成型出来ます。
次回はこの雌型を使ってカーボンFRPの作製を行います。 写真のとおり深さのある坪のような形状で曲面のかなりきついため積層に手こずりそうです。