今回の作業日誌は頼まれモノのアルミパーツ。
木工旋盤のスクロールチャックと木材間に使うアダプターの作製です。
今回の依頼
ご希望のパーツはこのような形状のアダプター。(アルミの円盤状のモノが完成品です。)
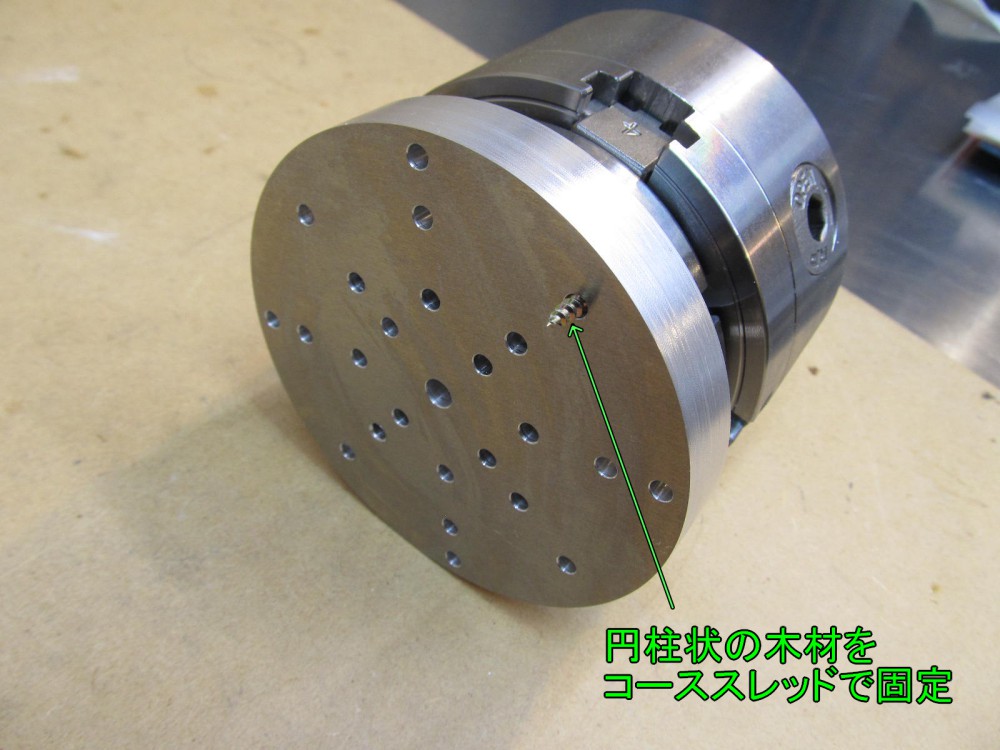
まず木材にアダプターをコーススレッドで固定してからスクロールチャックで挟んで使うらしい。(写真では1本だけですが4本で)
円筒状の木材から木製カップ、茶わんのようなものを作るときに使うアダプターとのこと。
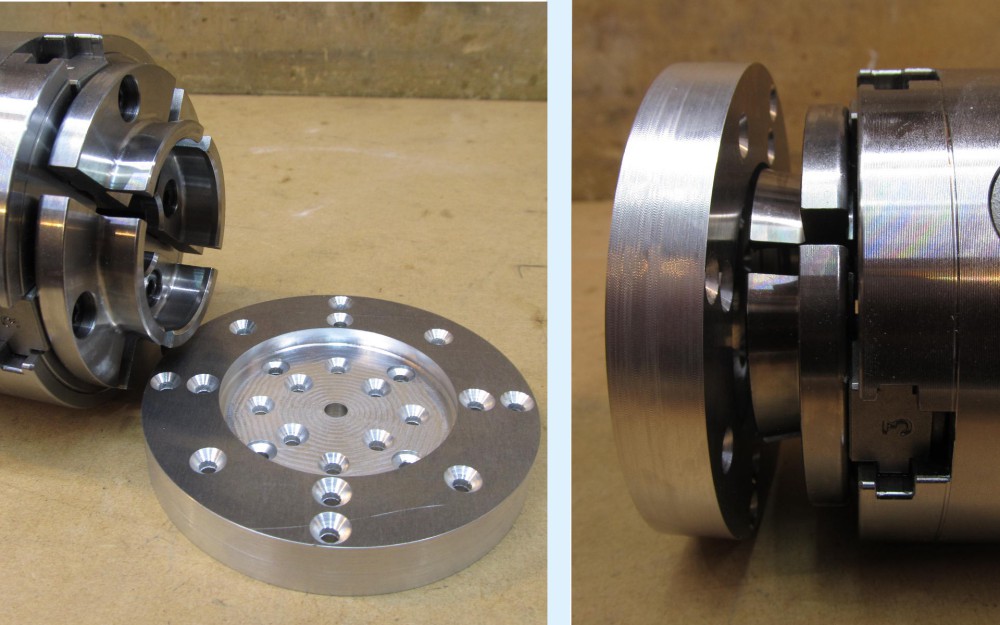
スクロールチャックのくわえる動作で簡単に脱着できます。
苦手なCNC作業を久しぶりに
手持ちの材料が15㎜厚のアルミ板しかありませんので板から切り出すのにCNCフライス盤を使う事に。
最近使っていなかったので活用するいいチャンスです。
「せっかく作った機械のため」というより「自分の技術を保ついい機会」です。(たいした技術ではありませんが・・・)
正直言いますとパソコンでCADで描いて・・CAMでNCデータを作って・・CNCマシンで切削するというステップがどうしても面倒に感じてしまうんです。
使えば手作業より美しいモノができるのことは分かっているのですがなかなか気持ちが乗らない・・。
頼まれると半ば強制的にやることになるので「いい機会、ありがとうございます」なのです。
さて、CADで描いたパーツがこちら。 面倒といいましたが描くのは簡単なパーツでございます。
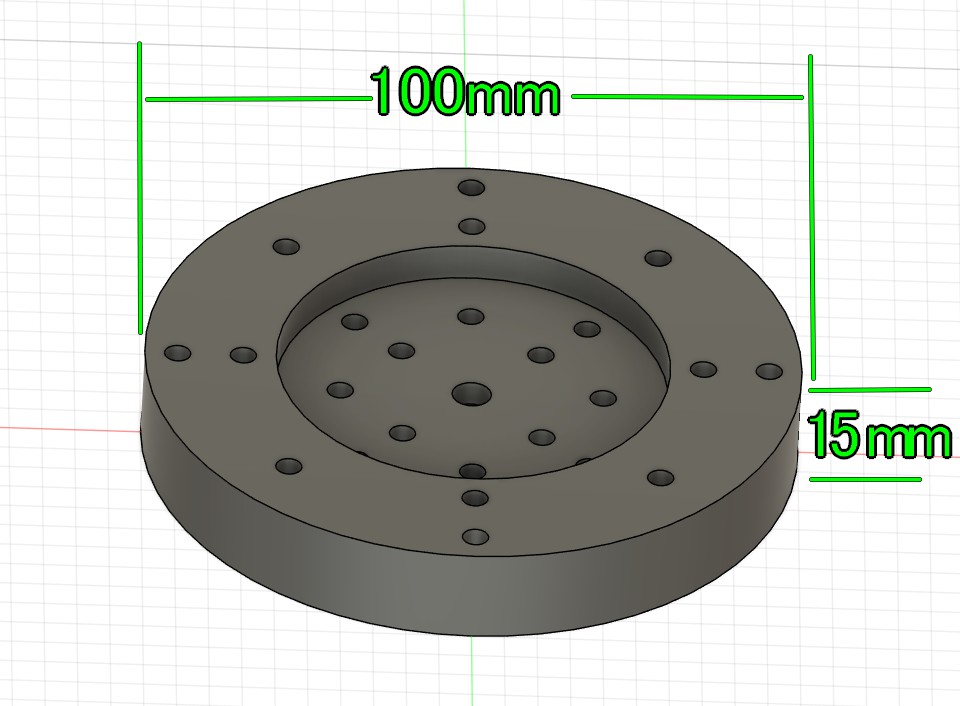
こちらをCNCフライス盤で切削すると・・・・
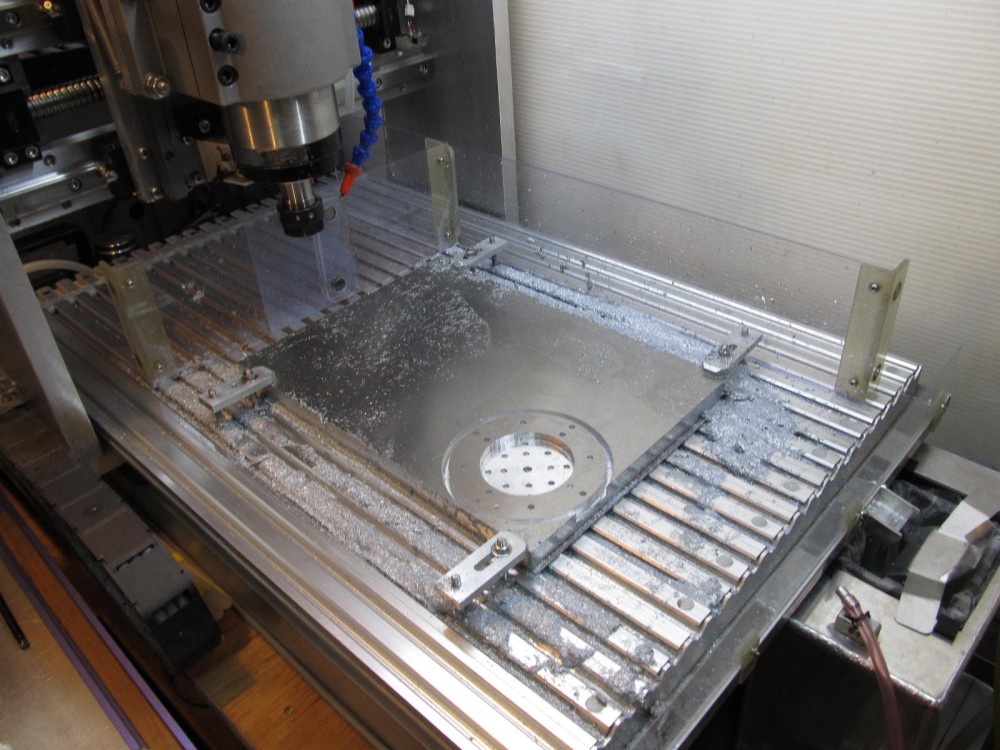
あーら簡単、もうできちゃいました! とはいきません。
ごらんのとおり切削屑だらけで結構あと処理が大変なんです。 これが億劫になってしまう一因です。
材料の種類、切削条件によりますが、細かい針状の屑になることもありそれが手に刺さって結構不快。
このアルミは硬質な感触なのでA5083のようです。(だいぶ前に購入して印をしていなかったのでおそらくです。)
これまでA5052の切削が多かったので気づきませんでしたが、A5083だと切削屑が鋭利になるようです。 ちくちく刺さります。
A5052の場合、後片付け時に刺さって痛い!ということはありませんでした。切削屑を手で触っても濡れたアルミの砂のような感触で楽しいくらいでした。(笑)
ですが、今回の切削屑は素手で触れませんでした。 お掃除はゴム手袋装着が必須。
ちくちくする切削屑を回収しながら切削する方法はないかな・・とまたまた工夫したいことが発生です。
快適化をはかりCNCフライス盤を気楽に活用できるよう精進します。
初歩的なミスで切削が途中で終了
先の写真、円盤が切り出せたようにみえますが失敗に終わっています。
コレットチャックの締めが甘くエンドミルが最後の外周切削に引っ込んでしまいました。
こんなイメージです。
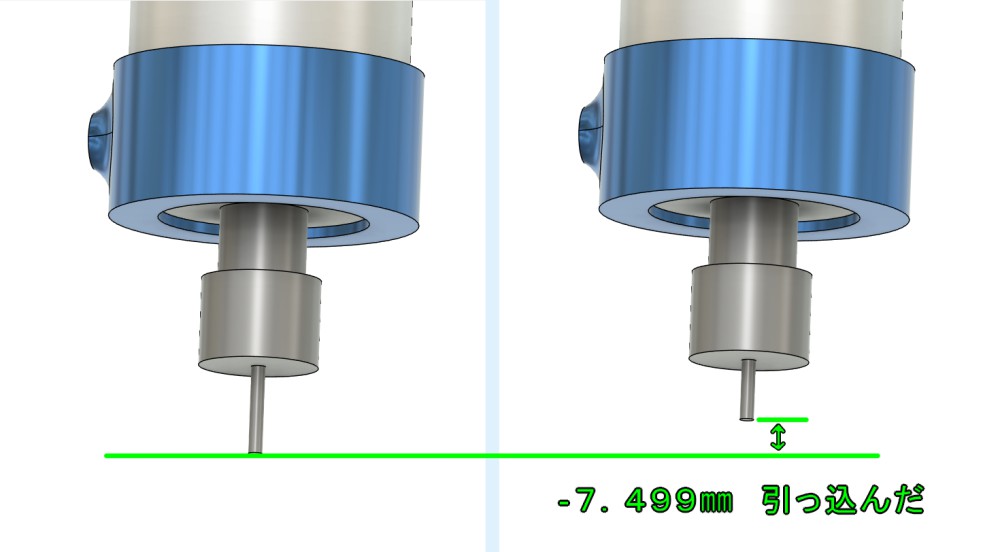
後で計測すると7.499㎜ひっこでしまいました。
切削後エンドミルを原点である「材料の上方1.0㎜」に持っていきました。
写真は、材料とエンドミルの隙間が1.0㎜の状態です。
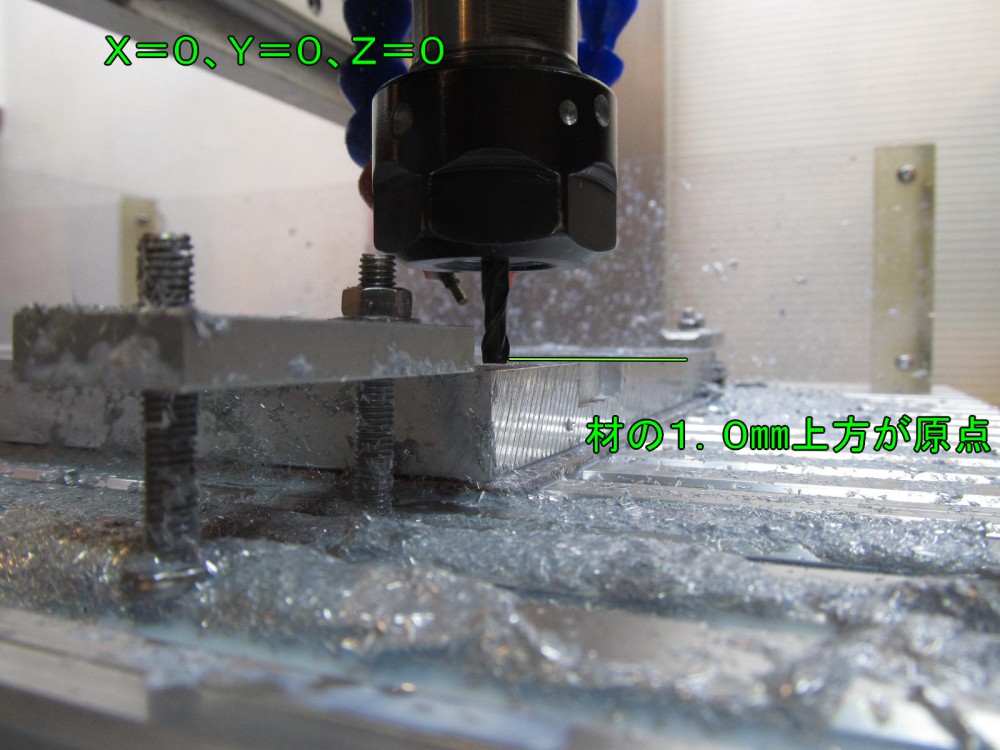
この状態でCNCソフトを見ると、Z軸だけ-7.499㎜を指しています。
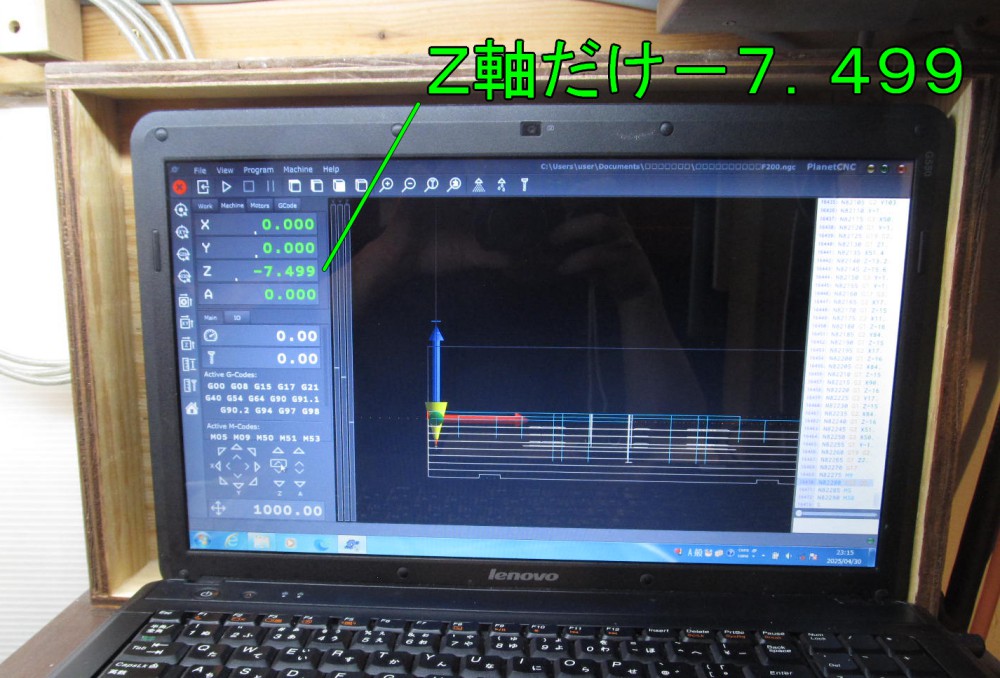
いや~がっかりでございます。
本音はやり直したい。(失敗したら1からきれいにやり直したくなる性格です)
ですが、「修正してやり抜くのもいい訓練」と思い作業を続けます。
修正作業
バンドソーでカクカクと外周を切り出します。
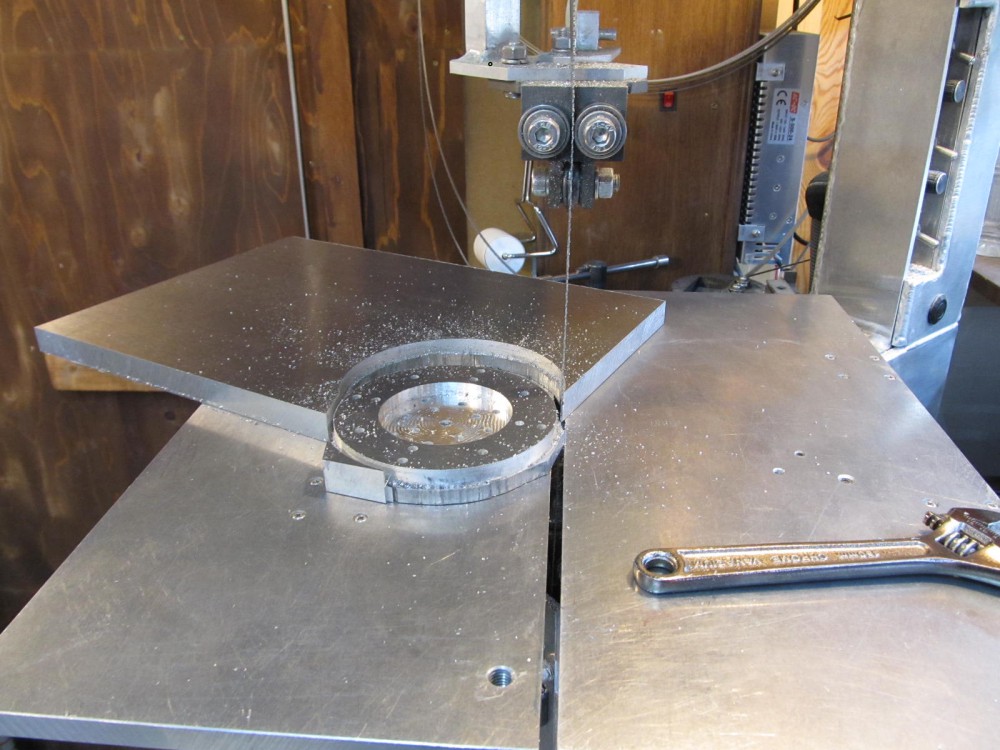
旋盤で凸凹の外周を均します。
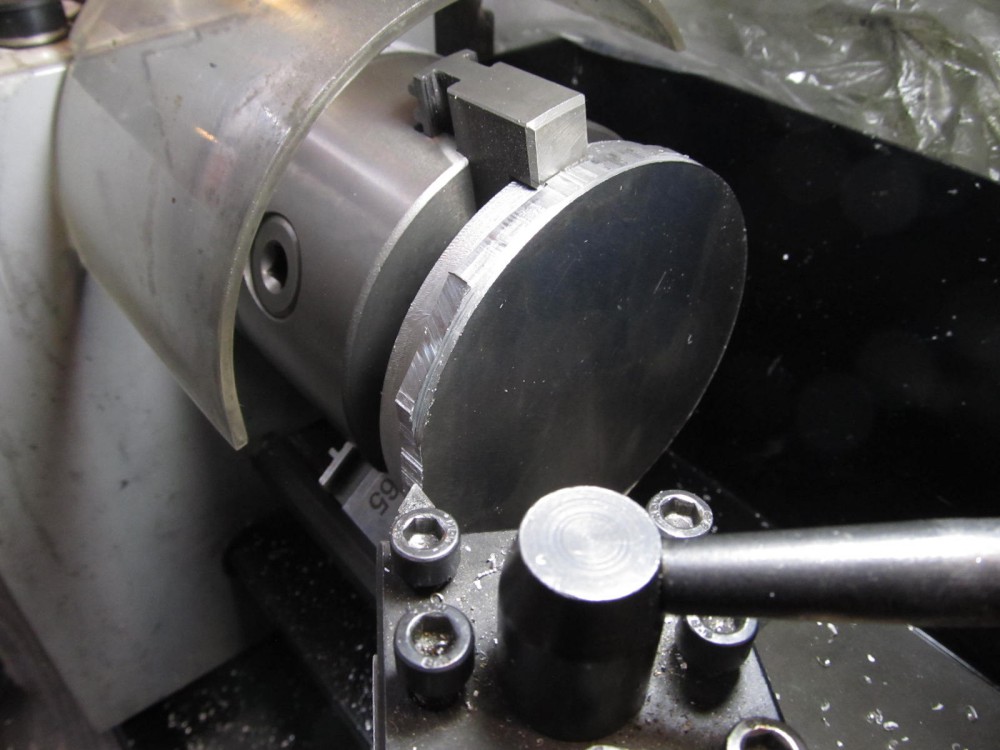
反転させてくわえ直しておりちょっと段差が出来てしまいますが、このパーツは外径の適当でも大丈夫なので妥協します。
外周を修正後、内側を逆テーパー状に切削して木工用旋盤のチャックの角度に合わせます。
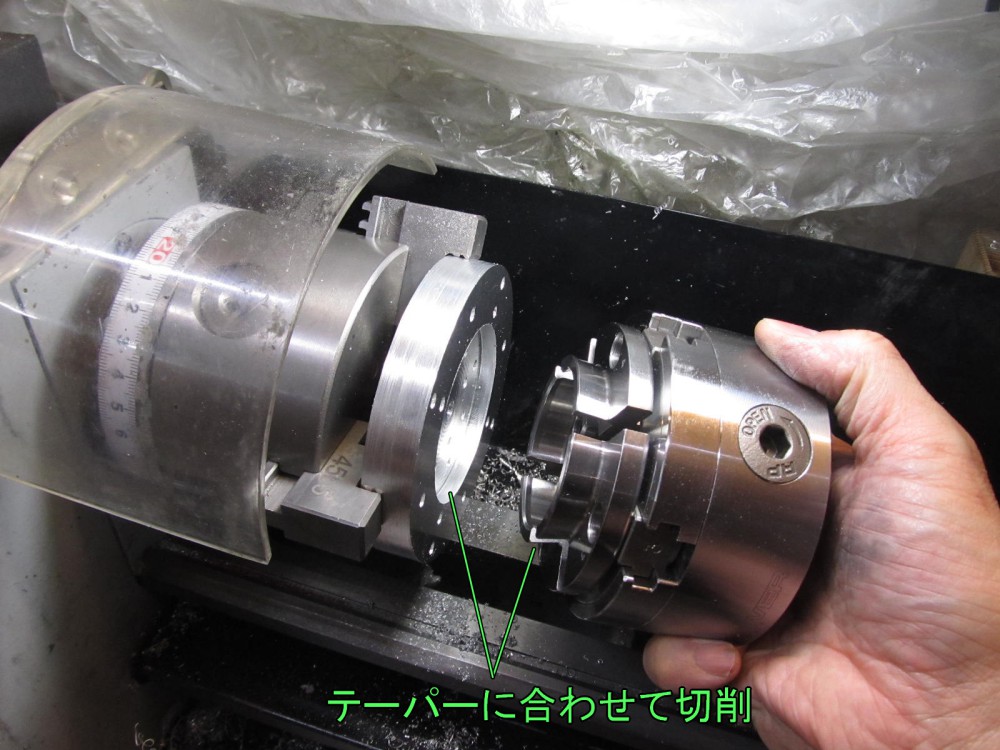
CNCフライスは3軸なので逆テーパーは切削出来ないんですよね。 いつかは5軸フライスです!
仕上げは手作業で
コーススレッドの穴開けと面どりは手作業です。ボール盤作業。
CANで描いた放射状の穴は深さ6mmまでになっており貫通しておりません。 これはドリルの下穴代わりです。
これで正確に指定の場所にボール盤で穴あけが出来ます。
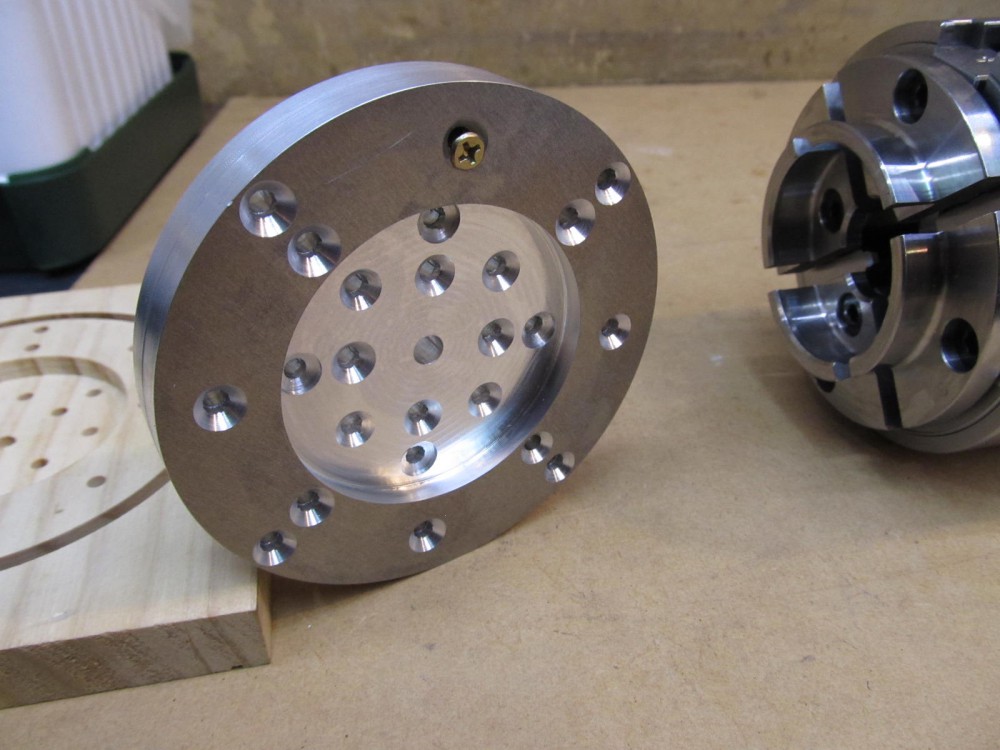
面取りカッターでコーススレッドが埋まるくらいに座グリして完成です。
面取り深さは手作業なのでまちまちですが、放射状の穴位置が揃っているとキレイに見えます。
よく出来ました!