多大な時間を要しシリコン型が出来ましたので、ようやくFRP成型作業に入れます。
今回の成型物は小型のAHDカメラのカバーなのでかなり小さくどうやって成型しようかちょっと悩みました。 サイズはタマゴくらいになります。
しかも入口より内部の方が広い逆テーパになっております。
ハンドレイアップで1層ずつ頑張ればいけるかな・・・?
型にぴったりフィットさせるのはインフュージョン成型に限るしなあ・・・。
でもインフュージョン成型は、この狭い空間にカーボンクロスやピールプライ、ネットを丁寧にセットして真空パックしなくてはならないし・・・出来るかなあ?
とまたまた思案してしまいます。
インフュージョン成型の準備
ちょっと面倒ですが、インフュージョン成型でいくことにしました。 カーボンクロス、ガラスクロスをセットしたところです。
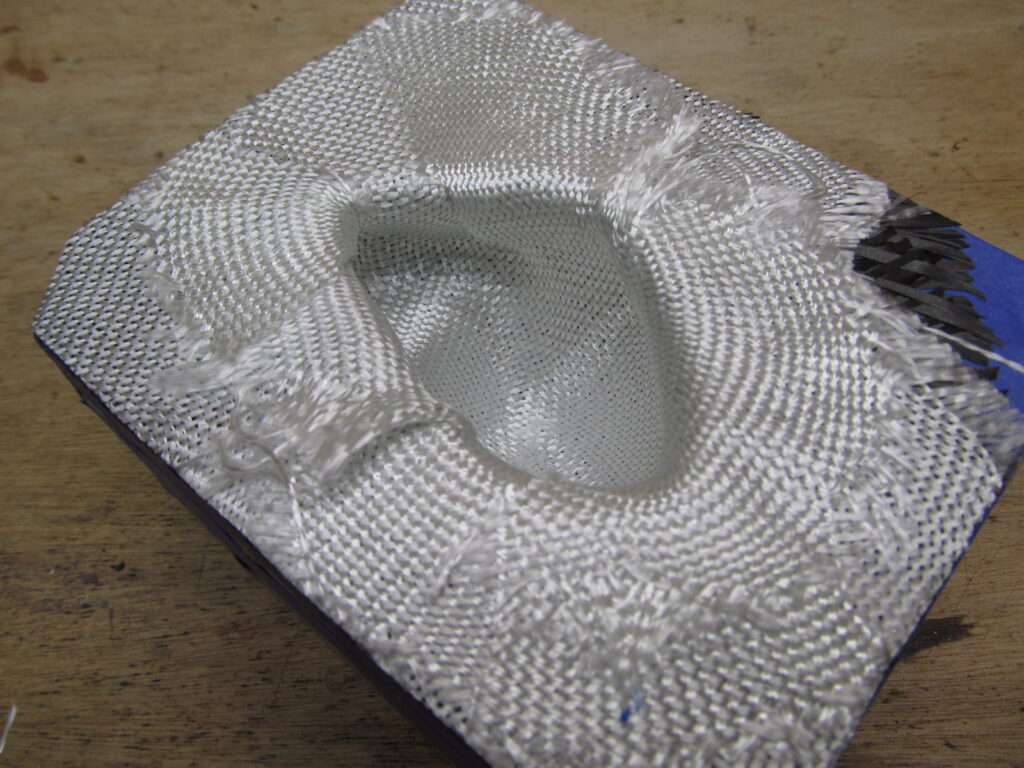
ガラスクロスの網目の大きさから型が結構小さいのがわかります。
カーボンクロス2層、ガラスクロス2層としました。 出来るだけ丁寧にクロスを変形させながら型にフィットさせましたが、本当に細部までクロスが密着しているのかはっきりわかりません。
指の感触だけで確認するしかありません。
さらにピールプライ + ネットを重ねます。
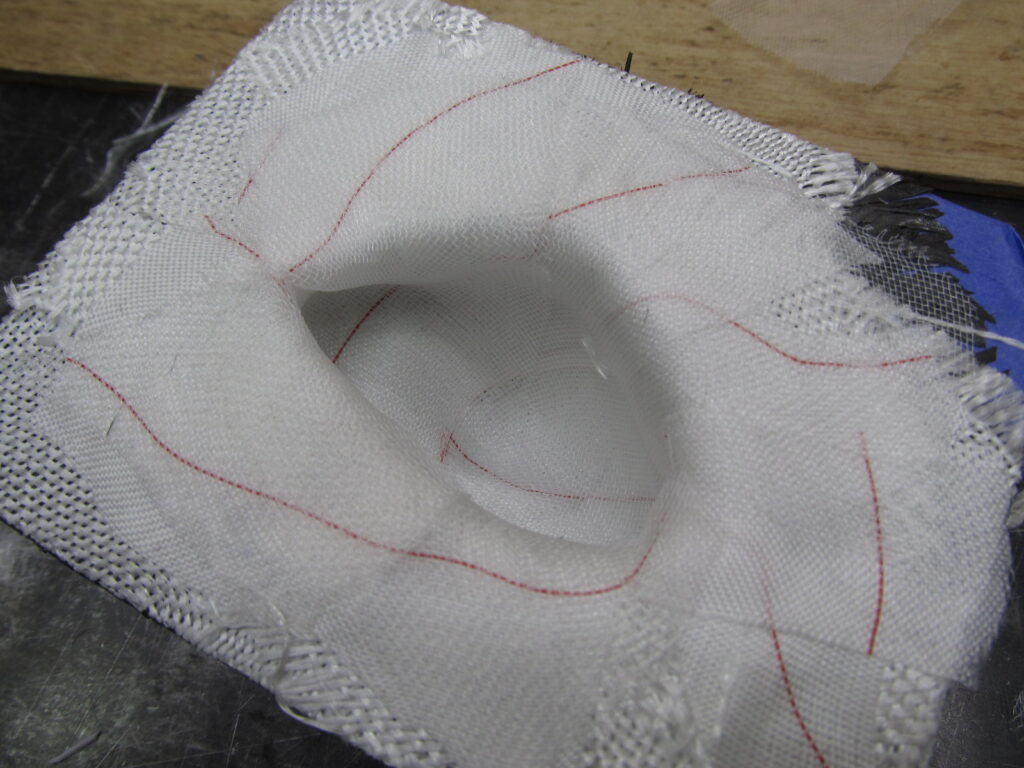
狭いところに無理やり布を押し込めた様になり「こんなんで大丈夫なのか?」と不安になります。
カーボンクロス2層、ガラスクロス2層、ピールプライ、ネット、と6層重ねたことになります。
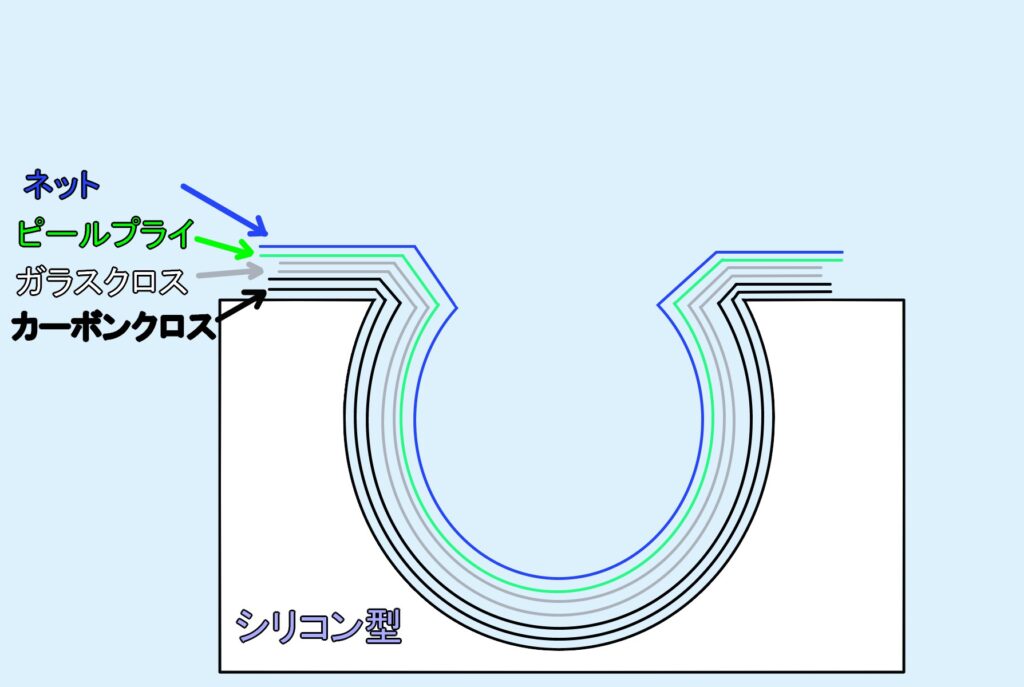
図にすると断面はこんな感じ。 6層をきれいに密着するようセットするのが大変なんです。
ハンドレイアップでは無理かも
このように逆テーパーかつ曲面がきつい型にクロス類を密着させることは、ハンドレイアップではほぼ不可能です。
こうやって押し込んでセットしていると、「ああ、クロスの元の形に戻ろうとするが結構あるからハンドレイアップでは密着させられないなあ」と実感しました。
そして、これを真空パックしますとさらに無理やり感がアップします。
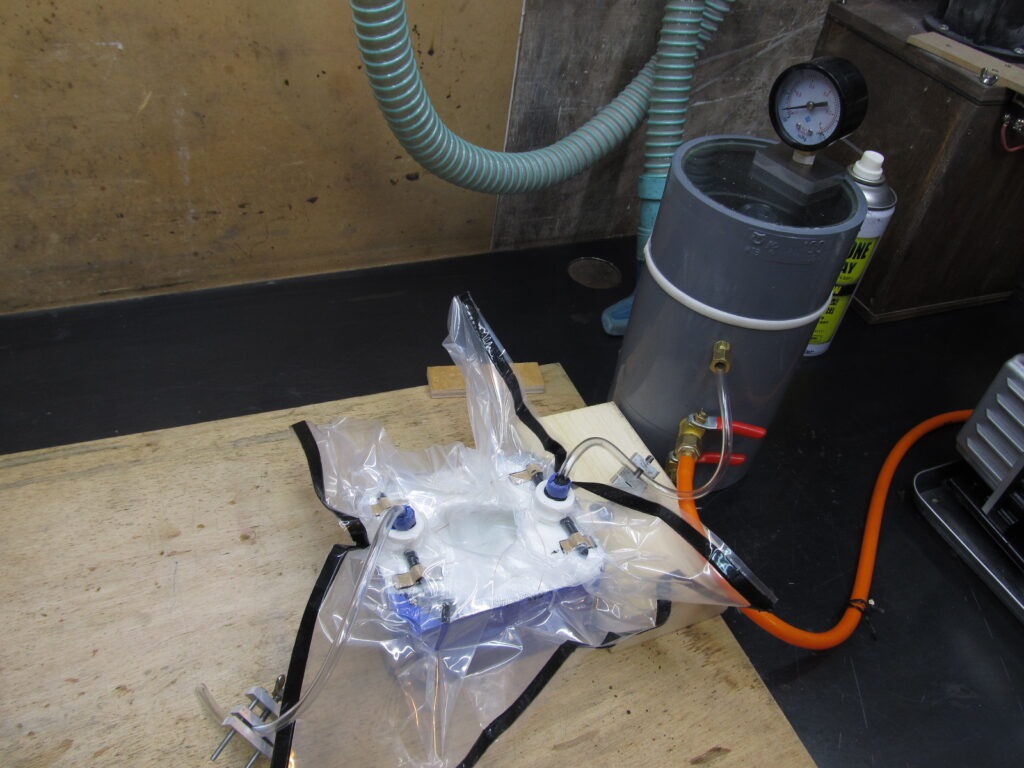
型に密着させるためポリ袋はたくさんのヒダを付けて押し込んでいます。
真空ポンプを止めてバキュームゲージが変化しないことを確認します。エア漏れがなければ樹脂含浸スタートです。
トータルではインフュージョン成型は早い
ここまでのセットが大変ですがここからが早いんです。 このサイズなら数分で樹脂含浸は完了します。 4層を数分で積層したことになります。
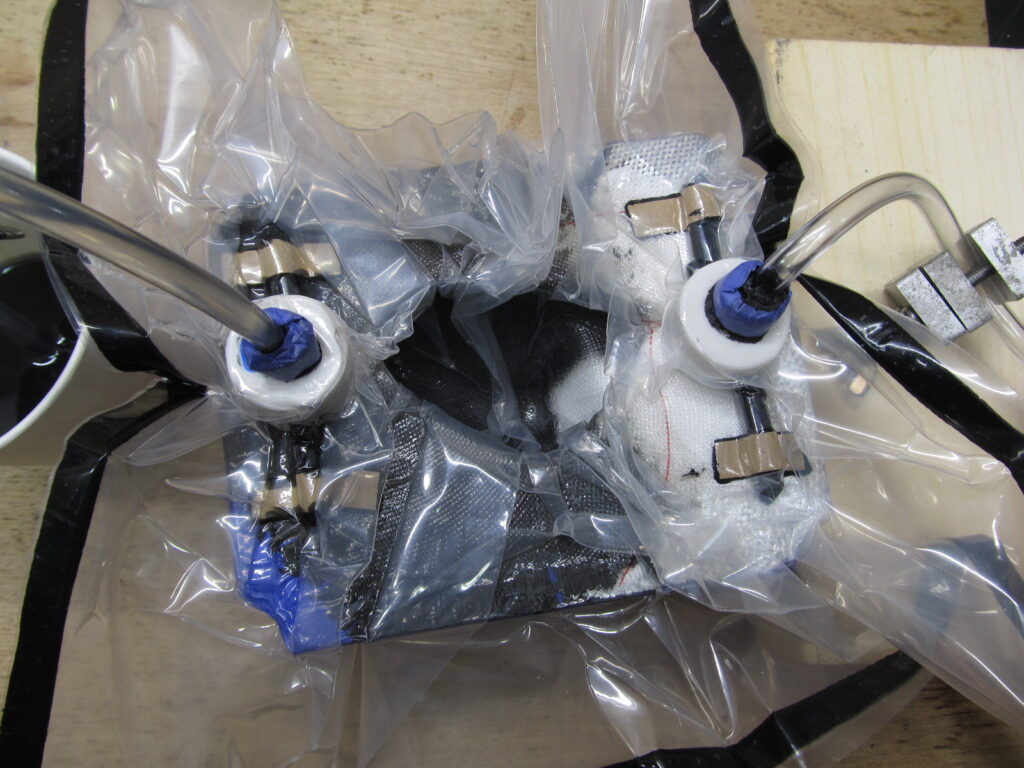
左のチューブから樹脂が流れ込んでいきます。右のチューブが真空チャンバーにつながっています。
真空パックまでの手間が初めにあるので「面倒くさいなあ」としり込みしていしまいますが、毎回ひしひしと感じるインフュージョン成型のいいところは次の2点!
① タイトな曲面でも型に合わせた積層ができる
② 樹脂で手が汚れない。樹脂に触れるのは硬化剤の混合作業時のみ。臭い匂いも短時間。
このようにピッタリフィットした積層はハンドレイアップではムズカシイ。
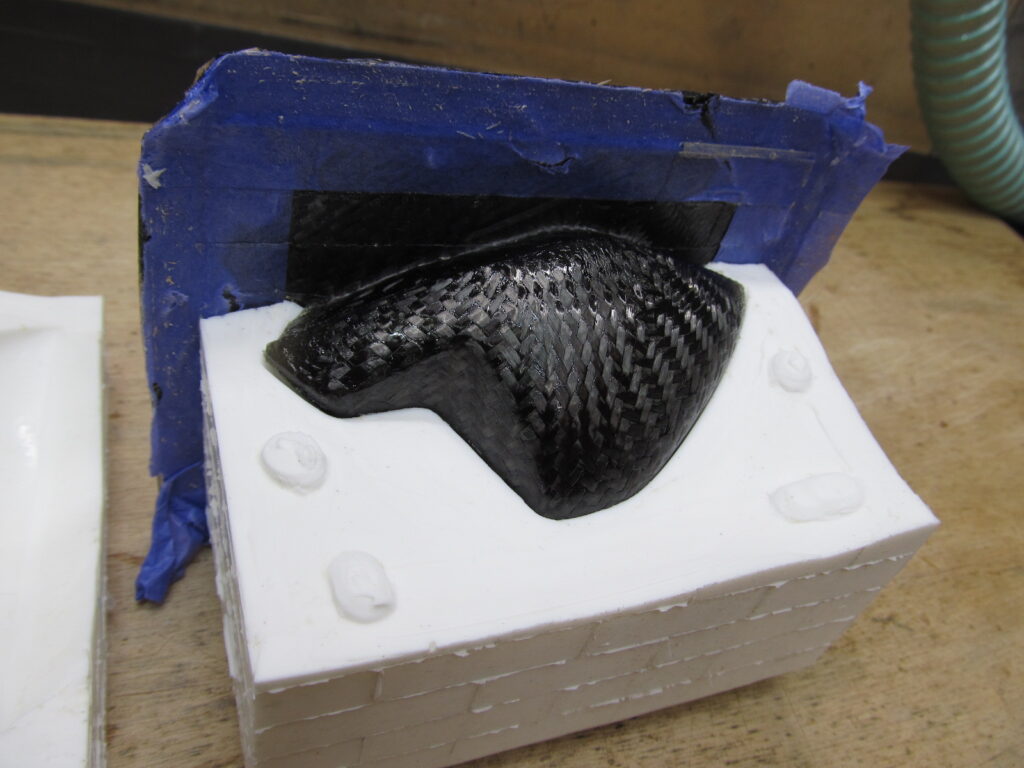
ちょっと凸凹てかてかしていますが、アセトンで拭いてクリア塗装すればきれいになります。
クリア塗装といってもさらに透明ポリエステル樹脂(積層もポリエステル樹脂使用)を塗布して研磨することが多いです。
今回はたまごサイズの小さなパーツなので余っていたUVレジンをテロテロ~と垂らして紫外線ランプで硬化! としました。
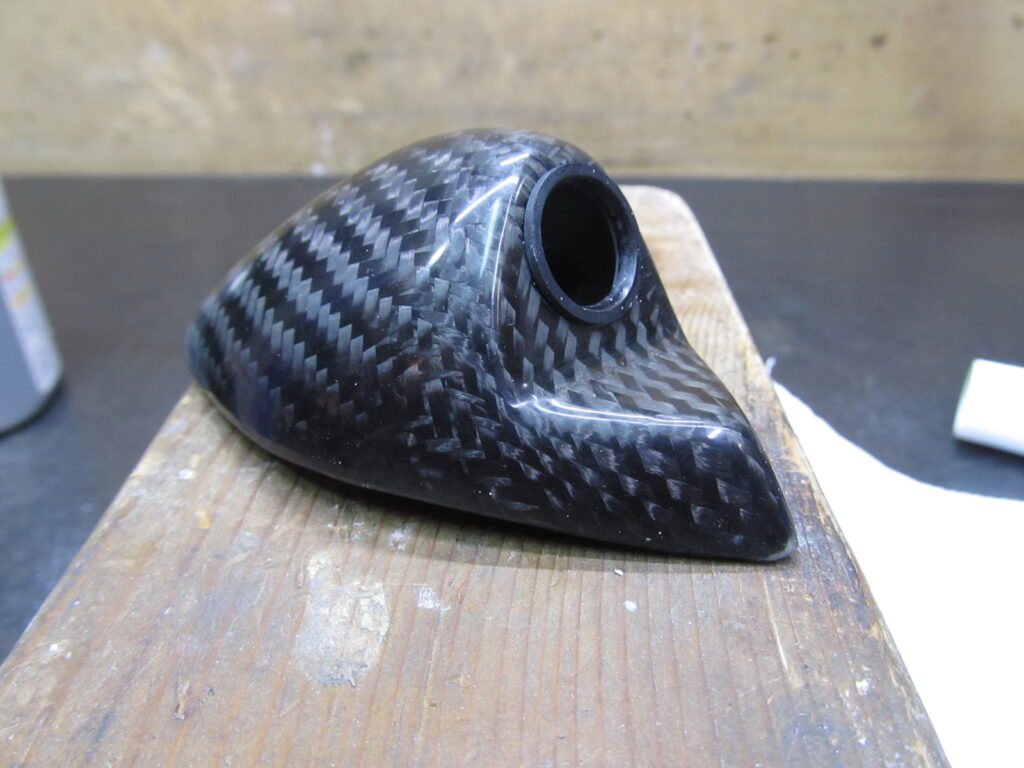
アクセサリー用の一般的なUVレジンですが、透明感がなかなかです。 紫外線による黄変も少ないらしい・・(商品説明によると)
これでカメラをサイドミラー下に固定できるようになりました。
あとは最後の難関「ドアパネルの取り外し」と「サイドミラーの取り外し」が待っています。