本日の作業日誌は、動力部分の組み立てとブレードのひねり機構です。
主軸ベアリングホルダーの固定
本体アルミケースからアルミ丸棒で4本足を出します。
ベアリングホルダーの位置と4本(写真ではまだ3本)のアルミ丸棒の位置関係が不規則に見えますが、実際に不規則です。
あえてデザインしたわけではなく、「モーター、タイミングプーリー、タイミングベルトの長さ」から導き出された結果でございます。
購入した部品を配置したらこうなってしまった、というのが正直なところ。
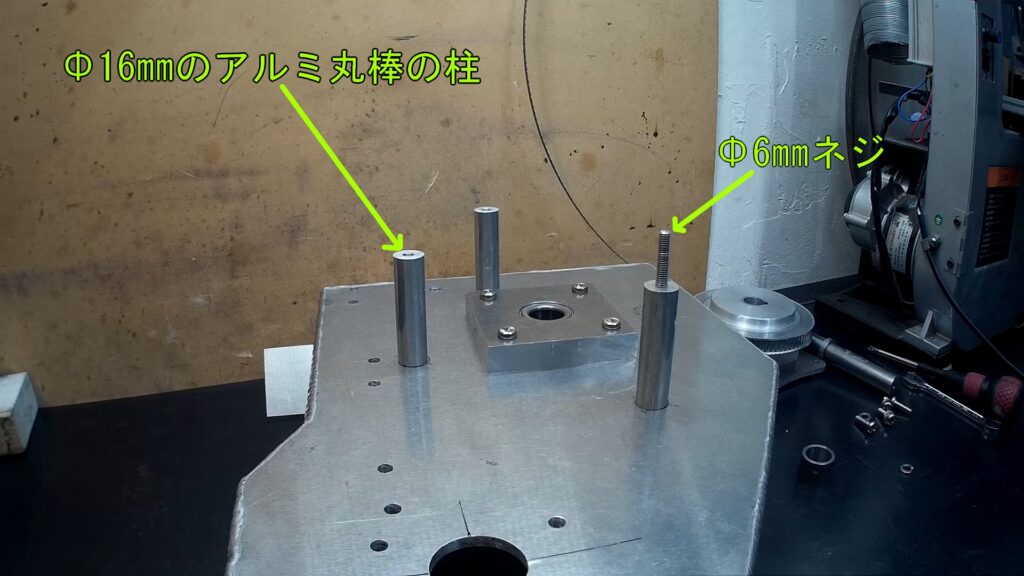
主軸ベアリングの一つは本体に、もう片方のベアリングはアルミ丸棒でかさ上げして固定。
基板スペーサを使ったかさ上げ(電子工作)のデカいバージョンですね。
主軸はΦ20㎜の鉄丸棒
柔らかいSS400材にキー溝加工を施したモノです。 キー溝は昔作った自作CNCフライス盤で掘りました。
CNCフライス盤はアルミ切削用として作ったので、鉄の切削するほどの剛性はありません。 そのためできるだけ柔らかい素材を・・・ということでSS400を使用しています。
キー溝用のキーがAmazonで普通に売っていました。驚き! 昔は入手が難しかった部品も簡単に入手できるので工作の範囲が広がっていきます。 嬉しいです。
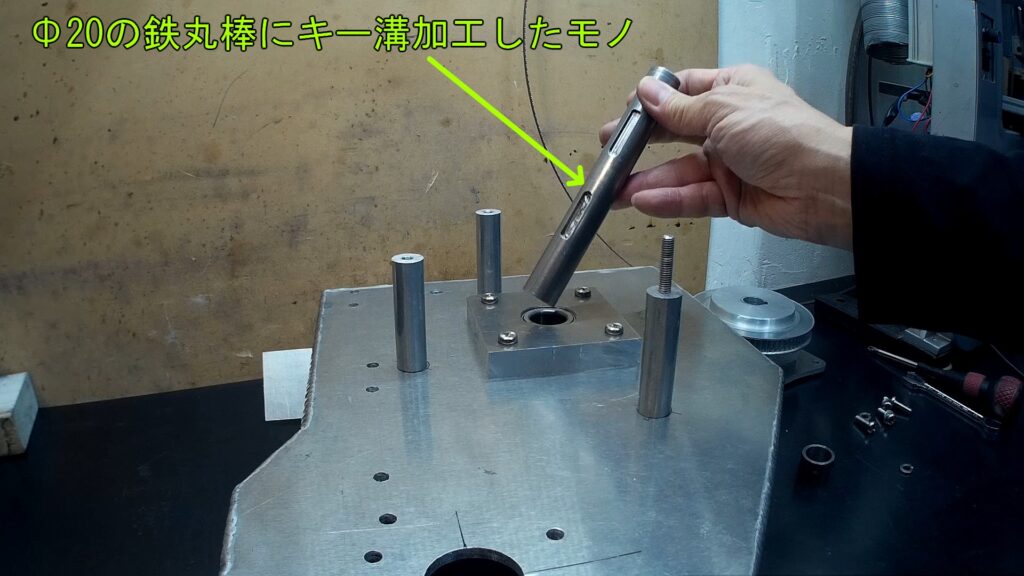
仮置きするとこんな感じです。
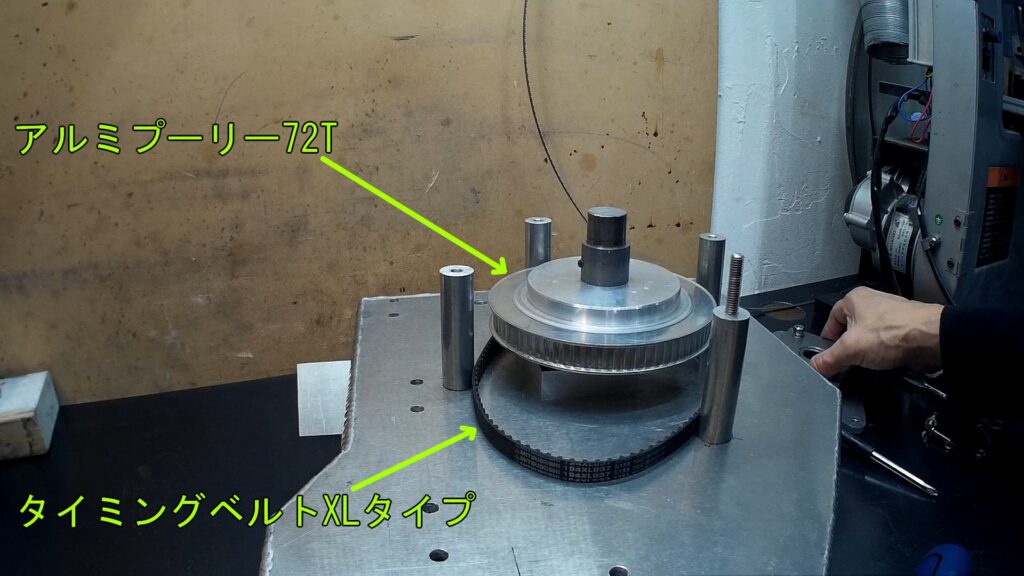
アルミプーリーはAmazonで販売されている一般的なモノですが、そこそこの動力を伝達するのでXLタイプと呼ばれる歯のピッチが5.08㎜のプーリーです。
ネットの画面上だとルックスがそっくりな2GTというタイプもありますがサイズが全然違います。 2GTの方が多くヒットすると思います。
2GT = 3Dプリンター等の精密な動きの制御用。
XLタイプ = 駆動力伝達用。
といったイメージでしょうか。
ベアリングは一直線上かな
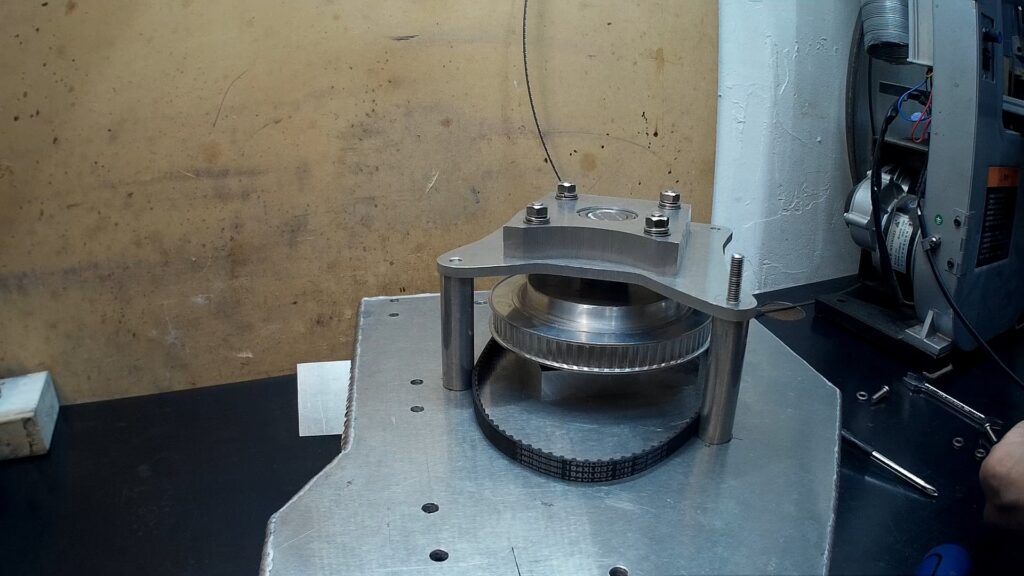
上下のベアリングと固定して滑らかに回転することを確認します。 フライホイールのようにいつまでもクルクル回ってくれるとホッと一安心。
azarashi工場長の技術では、部品たちが一発でピッタリと収まることはありません。
金属加工時には、Φ6㎜ネジ用穴は6.2㎜~6.5㎜ドリルで加工し、工作精度の悪さを吸収するようにしています。
モーターの取り付け
自転車用モーターを仮置きしてみましょう。
モーターのベースは「5㎜厚アルミ板に10㎜アルミ角材をコの字状に固定」したモノ。
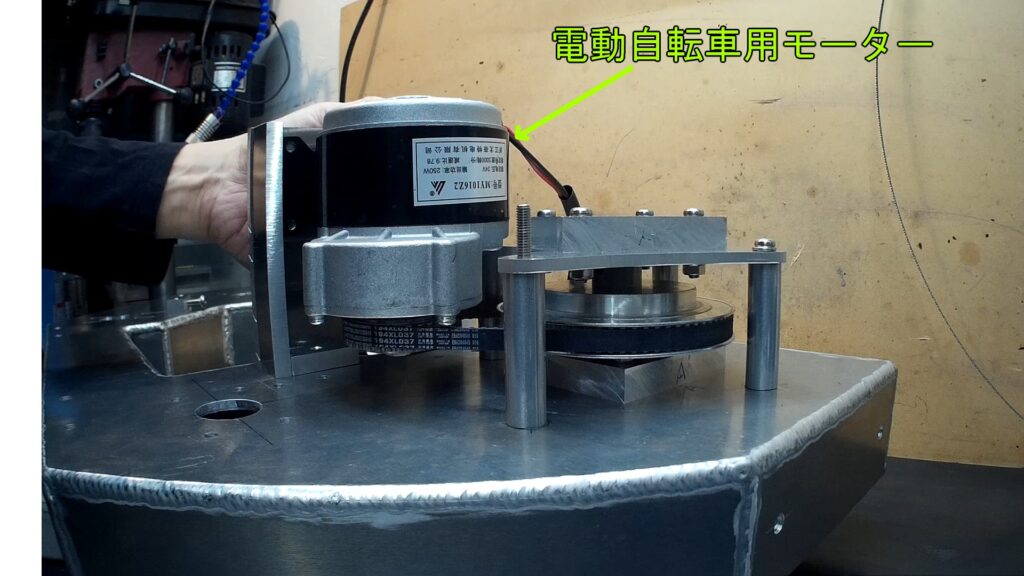
本体への固定用に、矢印の位置(両サイドのアルミ角材)にΦ8mmのタップ加工をしてます。
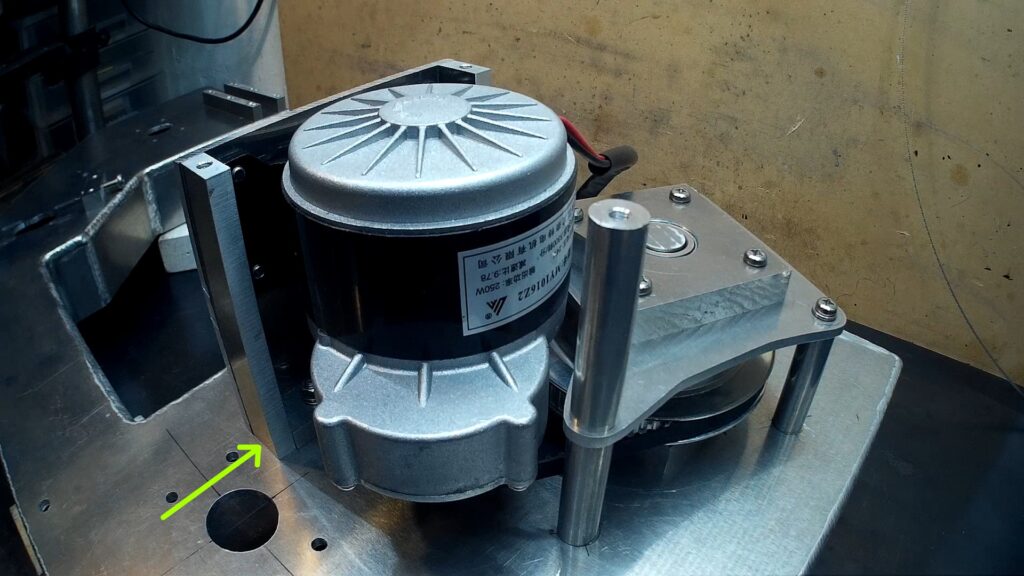
お察しのとおり矢印の箇所だけですと剛性がありませんので、ちゃんと3点で支えます。
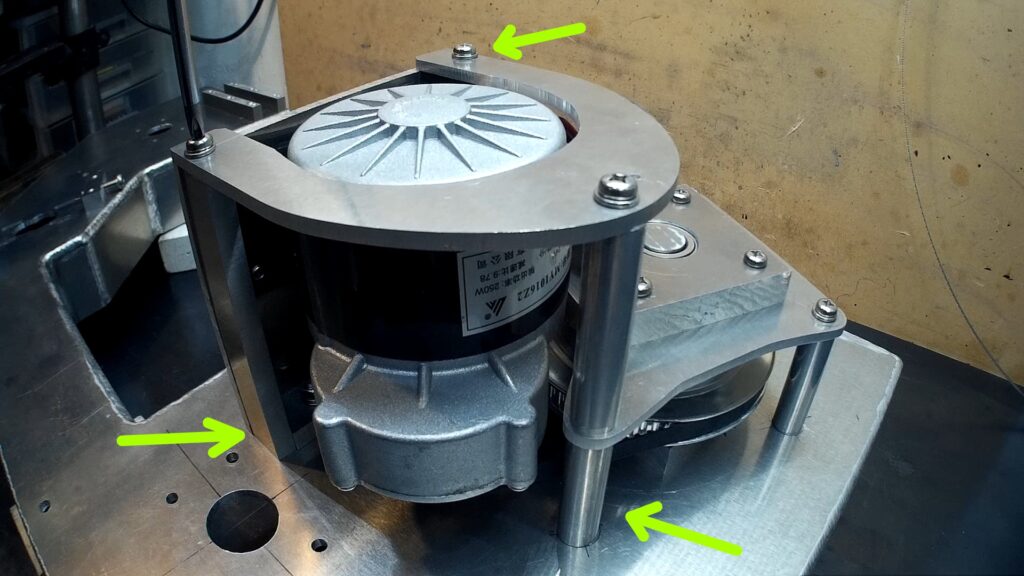
毎度のことながら「つぎはぎマシーン」ですね。 きっと2回3回と同じ機械を改良していかないと洗練されたデザインにはならないのでしょう。
あまり美を感じない構造ですが、私の力ではビクともしない剛性を感じます。 目的を果たしているのでこれで良し!
ブレードのひねり機構
本当の名称は知りません。 鉄パイプなど長物を途中で切断するためにはブレードをひねる(45度くらい?)必要があります。
工具鋼のブレードをひねりながら回転させるとは無理やりな仕組みだなあ・・・と思いつつ、海外youtuberのマネをして作ってみました。
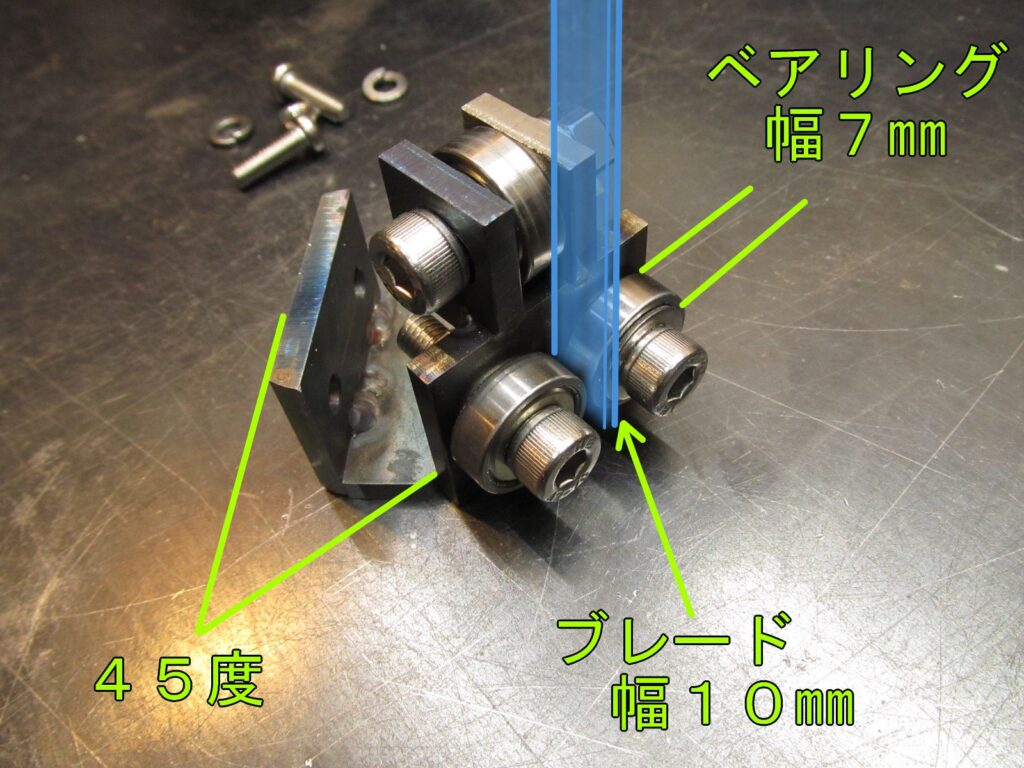
10㎜幅のブレードを使用するので刃の部分にはベアリングが当たらないよう7㎜幅のベアリングを使用しています。
使用するブレードによってベアリング厚を調整する必要ありそうですが、おそらく10㎜幅ブレードのみを使っていくと思います。
〇 ベアリングは「内径8㎜、外径22㎜、厚さ7㎜」のベアリングを3個。
ひねり機構は上下2か所あるので合計6個。
〇 ベアリングの軸は、Φ8㎜の六角穴付ボルト。
ネジ穴は、ベアリングの位置調整用にたて長に加工してあります。
〇 フレームは5mm厚の鉄フラットバー(ミガキ材)製。
フラットバーからバンドソーで切り出してTIG溶接で組み立てたモノです。
組み立て前はねずみ色のミガキ材でしたが、小さいパーツなのであっという間に溶接の熱で紫色~紺色に焼けました。
鉄やステンレスの熱で焼けた色っていいですね~! バイクのマフラーを連想させます!
溶接の強さを感じました
ひねり機構は力がかかりそうです。 鉄板つぎはぎ構造になってしまい強度が心配でしたが杞憂でした。
後からくっ付けているという作業から、「これまで使ってきたFRPなどの接着を連想」し接合個所の強度が心配になっていたようです。
溶接と接着は別物ですね。
1cmほどの溶接長でも人力は破壊できません。
スポットで溶接して位置確認 → あー失敗だ! となってもなかなか修正ができません。
今回の小物の作成をとおして、ちょこっとした溶接でも人力では破壊できない強度があることを実感ました。