ついに3Dプリンターを購入しました!
製品名 ANYCUBIC製 Kobra Max 印刷サイズ400㎜×400㎜×450㎜ の少々大き目の3Dプリンターです。
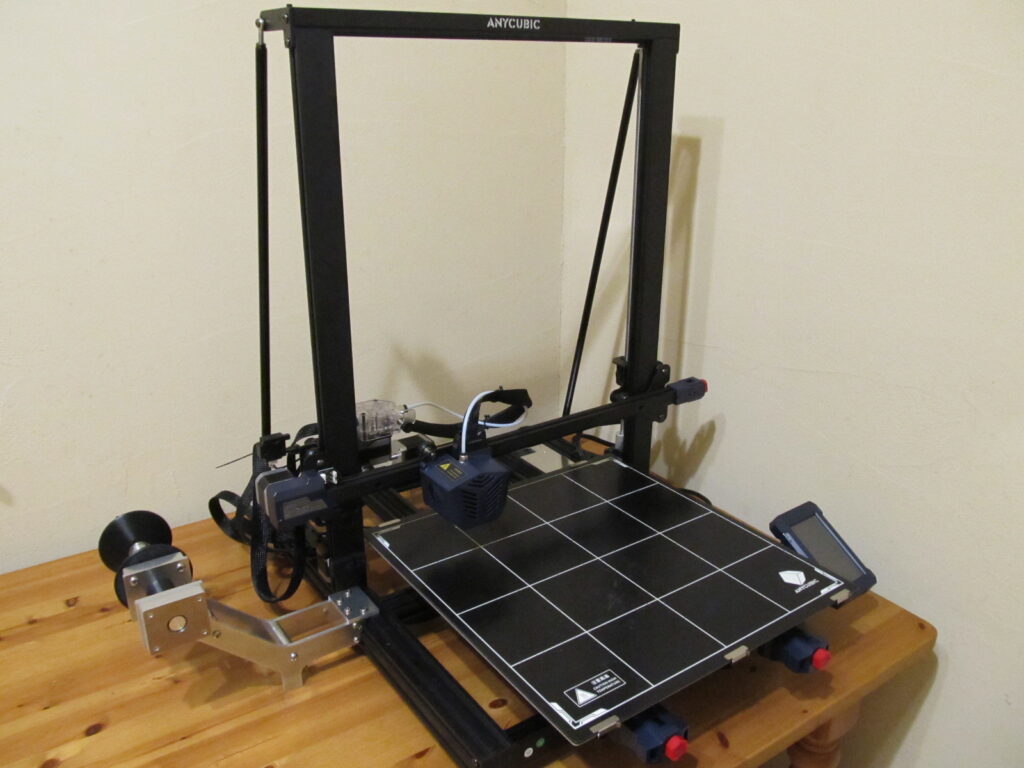
フィラメントタイプの3Dプリンターは比較的お手頃価格で販売されているなあと思いつつも、出力したモノの強度がなさそうで二の足を踏んでおりました。
これまでのFRP実験から「型を3Dプリンターで作成するべきでは」との思いがムクムクし、Amazonでポチることなりました。
やってみなければわからない。
まだまだ使い方を勉強中ですが、中国製なのか(偏見・・すいません)いろいろと気になる部分がでてきました。 さっそく改良です。
先に結果をご覧ください。↓ 滑らかに回転するホルダーです。
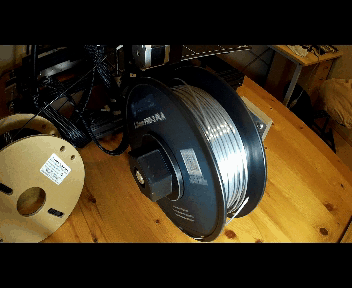
本記事を3分ほどの動画にまとめしたので、youtubeも参考にご覧ください。
目次
フィラメントホルダーが貧弱
フィラメントスプール(リールみたいなもの)を引っ掛ける純正パーツは樹脂製です。しかも片持ちなのでたわみます。
さらに、ただの丸棒なのでスプールが滑らかに回転しません。
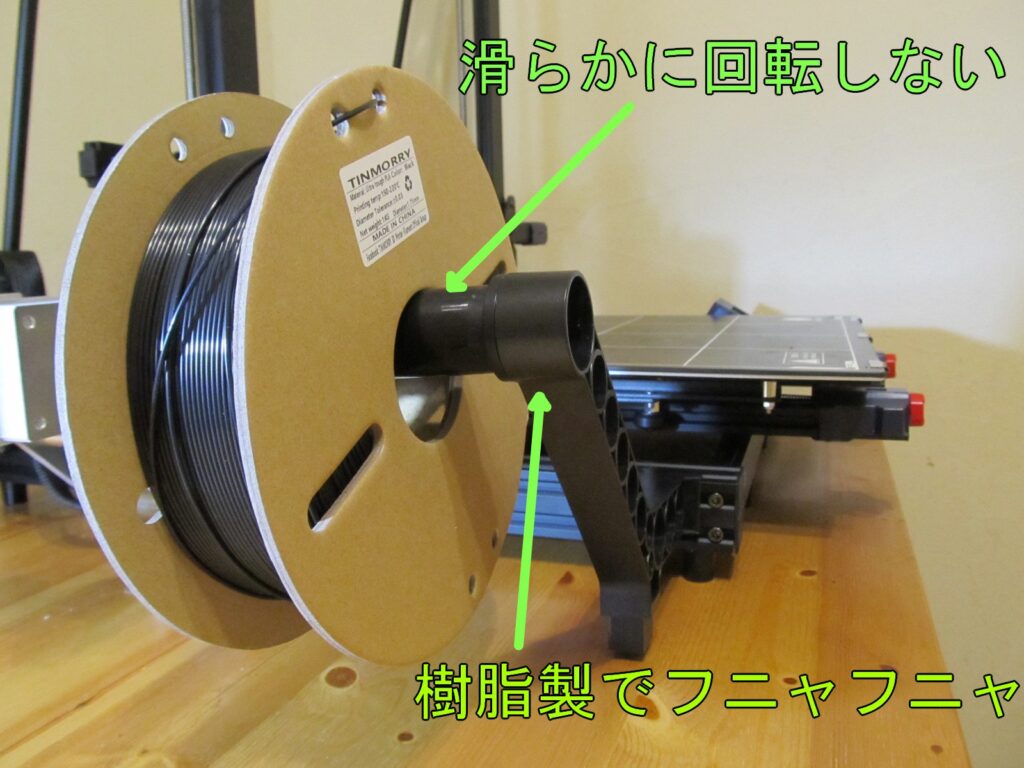
不満ばかり述べてしまいましたが、問題なく印刷しているのでこのままでも十分なのでしょう。メーカーさんがよしとして販売してますので。
しかーし、azarashi工場長としては、この作りに美を感じないのです。
重さ1kgのフィラメントがホルダーをユラユラとたわませ、フィーダーモーターが回転しない軸の摩擦に耐えてフィラメントを送っている、という苦しそうな状況に耐えられません。
そこで、アルミ製、ベアリング仕様のフィラメントホルダーを自作してみます。
主な材料はアルミ
フレーム部分 5㎜アルミ A5083
ベアリングホルダー 15㎜アルミ A5083
軸受け 内径16㎜、外径40㎜ベアリング
軸 直径16㎜アルミ丸棒 先端部分を旋盤でネジ切
コーン部分 PLA樹脂 3Dプリンタ出力
フレームの作製
フレームの5mmアルミ板はバンドソーで切り出しました。
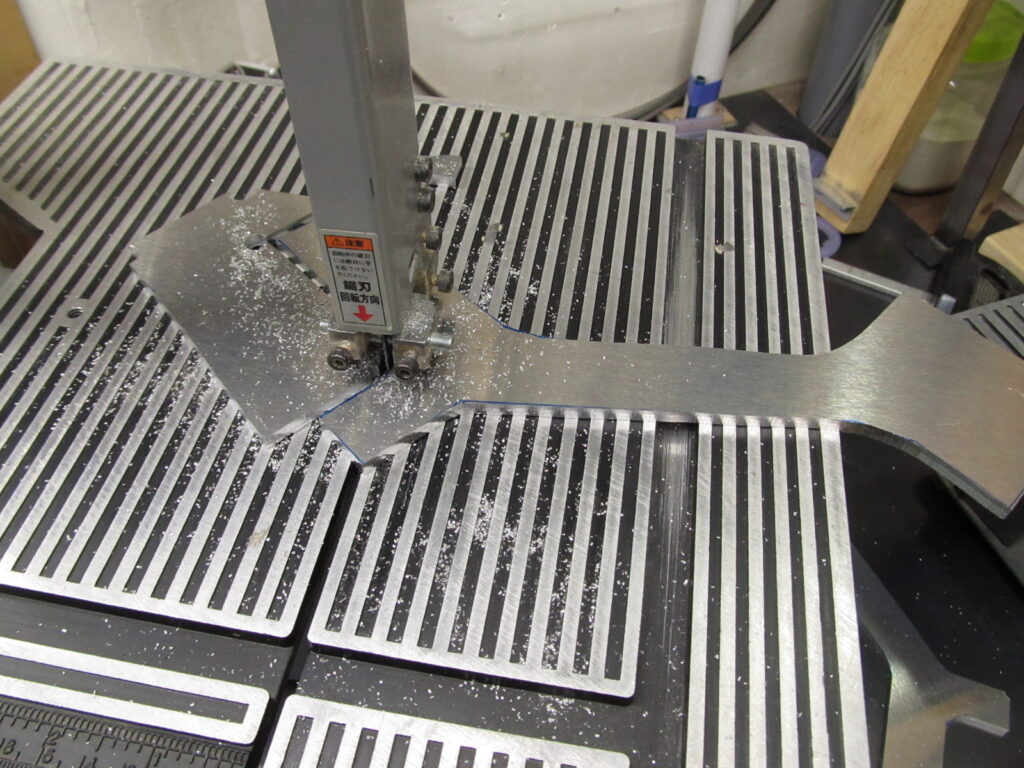
同じものを2枚切り出し後、ネジで仮止めしてベルトサンダーで外周を整えます。これで左右のフレームは同じサイズに。
左右のフレームはΦ16㎜アルミ丸棒で連結します。アルミ丸棒は旋盤でセンターに穴あけ後5mmのネジを切りました。
ベアリングホルダーの作製
15㎜アルミ板をパネルソーで切り出しCNCフライス盤でポケット加工しました。
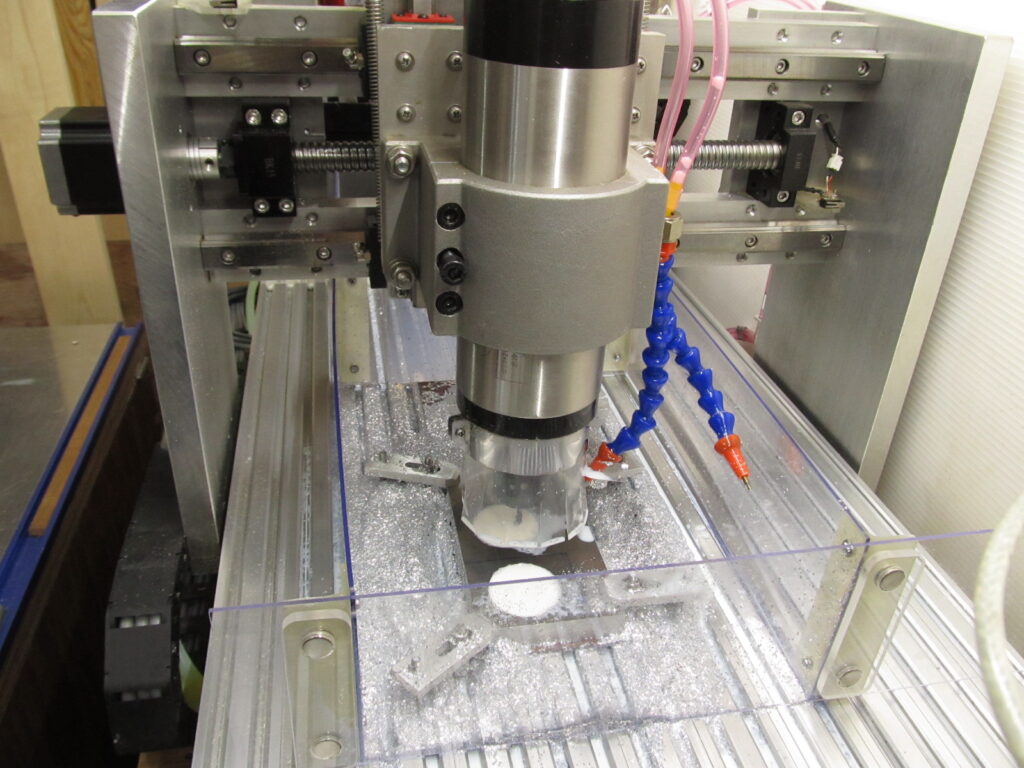
自分で作った工作機械が活躍してくれると嬉しいですね。この「CNCフライス盤」余り頻繁に使っていないのでかわいそうなのですが、たまに大活躍してくれます。(いつも泣いていた~トナカイさんは~、が頭に浮かびます。)
あと、日々活躍してくれる自作パネルソーもとても便利。刃を交換すれば金属もサクサク切断してくれます。
私の工作レベルではアルミの15㎜が気軽に切断できれば十分!
ちょっと話が逸れますが・・・
アルミ材へのねじ切り(深穴)について
今回の工作は、ベアリングブロックやアルミ丸棒へのネジ切が多数ありました。4㎜~5㎜の小径ネジなのでタップを折ってしまわないかと冷や冷やしながらの作業でした。
タップ作業って何度やっても緊張します。
タップを折らないために
深穴へのタップ作業でタップを折らないために気を付けていることをメモっておきます。
使用工具は以下の3点です。
・スパイラルタップ Amazonで販売されている安価なモノです。
・クラッチ付き電動ドリル(インパクトではない)
・ハンドタップ (比較的安価なライト精機の中タップのみを使用しています。)
ネジ切り手順
1 下穴はボール盤で開けておきます。5㎜ネジの場合、下穴は4.2㎜
2 スパイラルタップを電動ドリルでねじ込む。クラッチは弱めで。ドリルを持つ手に返ってくる反動トルクを感じながらねじ込みます。
余り反動が強いと当然折れます。どのくらいがいいかは、ハンドタップの経験から体得ってとこでしょうか。
またアルミの種類×ねじ径によってはスルスルとタップの最後までねじ切れることがあります。
その場合、最後に行きつく前にドリルの回転をストップさせないと折れる可能性大です。
タップ根本(ドリル側)が太いためこれ以上ねじ込めない・・・でもタップ部分は進みたい・・・と綱引き状態 → 根本からポキっとネジ穴に残ります。(泣きたくなります)
3 スパイラルタップで全部ねじ切る必要はない。
反動が強くこれ以上は折れそうと感じたら、そこまでで終了。ハンドタップに移行します。
4 一度ネジ穴を掃除してから、ハンドタップでチマチマとネジを切る。
「半回転→1/4戻し」(ときには1/4回転ずつ)、と反動トルクを感じながら・・・タップ折れに恐怖しながら・・・丁寧に進めています。
話は戻りまして・・・
軸の作製
軸はΦ16㎜のアルミ丸棒。フィラメントスプール固定部分にピッチ2㎜でねじ切りしてあります。
対応する雌ネジもアルミ丸棒Φ25から作製。この雌ネジを写真左側のコーンに打ち込んであります。
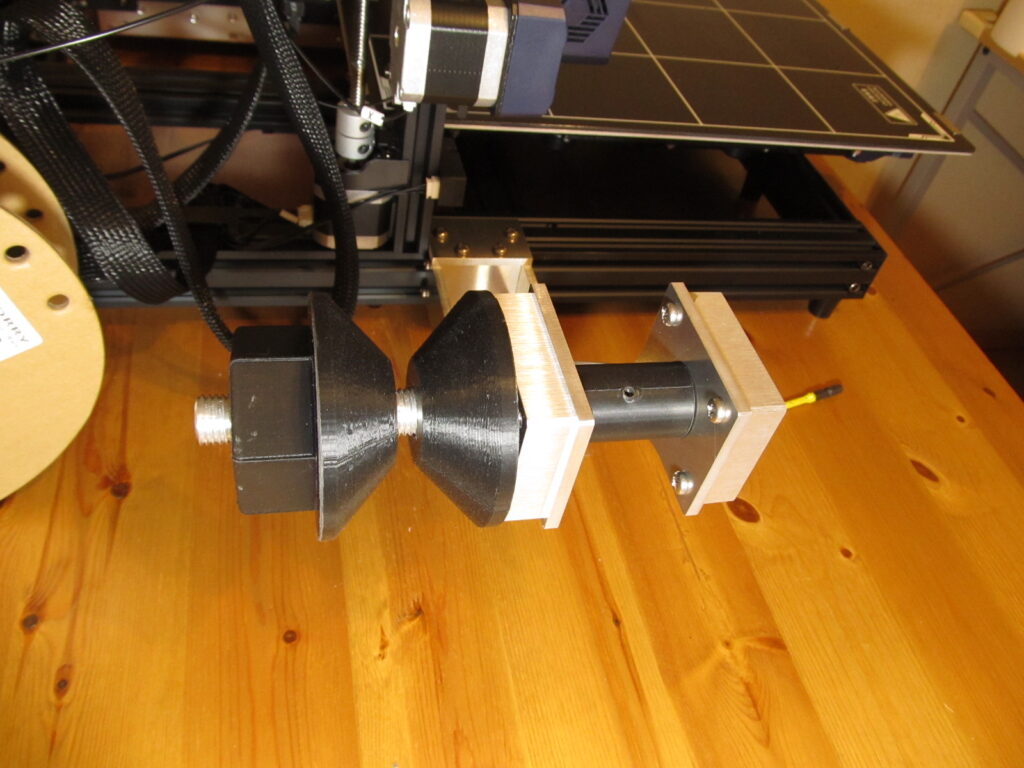
フィラメントスプールをタイヤに見立て、センターナット一つでタイヤ交換するF1をイメージしました。(笑)
写真左側のコーンが6角ナットになっています。
フィラメント固定コーンの作製
先の写真のとおり、様々な穴径に対応できるようコーンで挟む方法としました。
フィラメントスプールの軸穴はメーカーによってかなり異なります。
コーンのサイズは、3Dプリンタと合わせて試しに購入した5種類(1kgを4種類、250gを1種類)のフィラメントを基準に決定。
これで大体のサイズをカバーできるはずです。
で、コーンのサイズは・・・大きい方の直径80㎜、小さい方の直径36㎜。厚さ25㎜です。
3Dプリンターで出力
写真の黒いパーツは3Dプリンタで出力。
使用樹脂 高強度、高靭性PLAフィラメント TINMORRY製
「金属、FRPで作る必要がない、強度や耐熱性が要らない」部品の作成に、3Dプリンターはうってつけです。
簡単、スピ―ディ、ゴミが出ない。
円錐状のモノ、6角ナットなど単純な形状ならCAD作業も数分です。(素人でも)
パソコンでの作業は、fusion360で設計→STLファイルで出力→スライスソフトで読み込み→スライスしてGコードファイル出力、という流れを踏みます。
面倒そうですが、今回のコーンの場合のPC作業は10分くらいです。
最後に、作製したGコードファイルをSDカードにコピーし、3Dプリンタで印刷開始!
後はお任せとなります。 まあ、なんと便利な機械でしょう。
ただし、プリント時間はコーン1個につき2時間弱かかりますので、「遅いなあ~」なんて声も上がりそうですが、FRPですと「型作りやら成型やら」でどうやっても2時間では完成しません。
おまけに自分が作業しっぱなしになります。
便利な工作機械が増えました~。
パーツ完成
フライス作業、タップ作業、などなど苦労して完成した部品たちです。
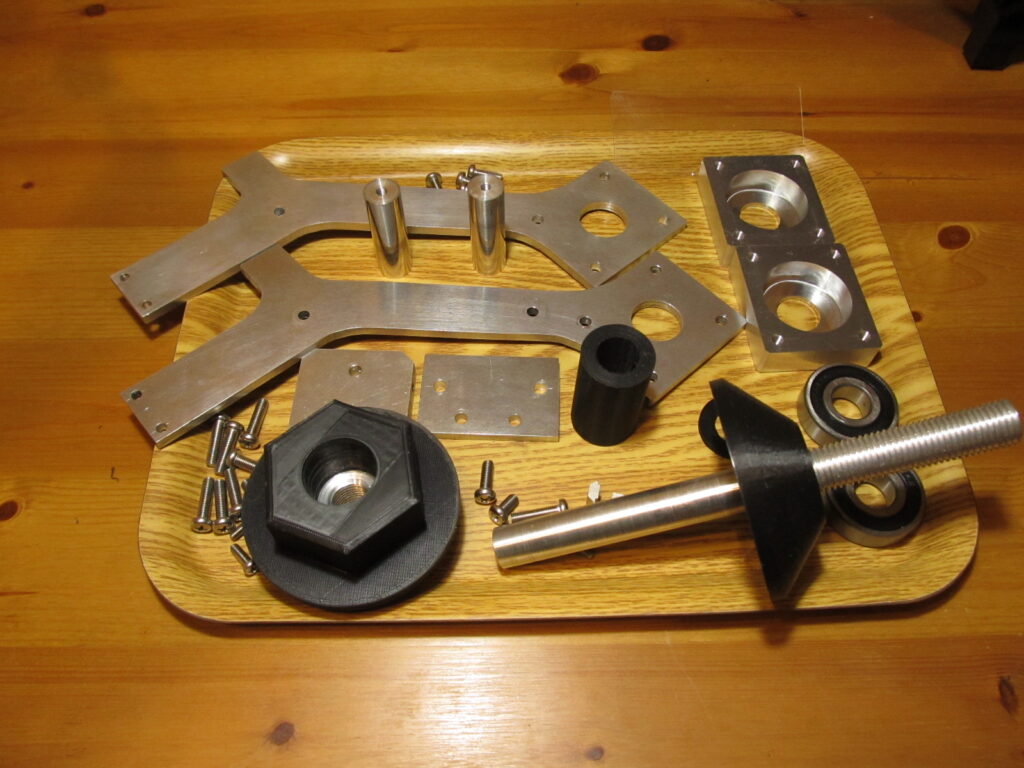
組み立ててみます。 ↓フレーム片側分です。
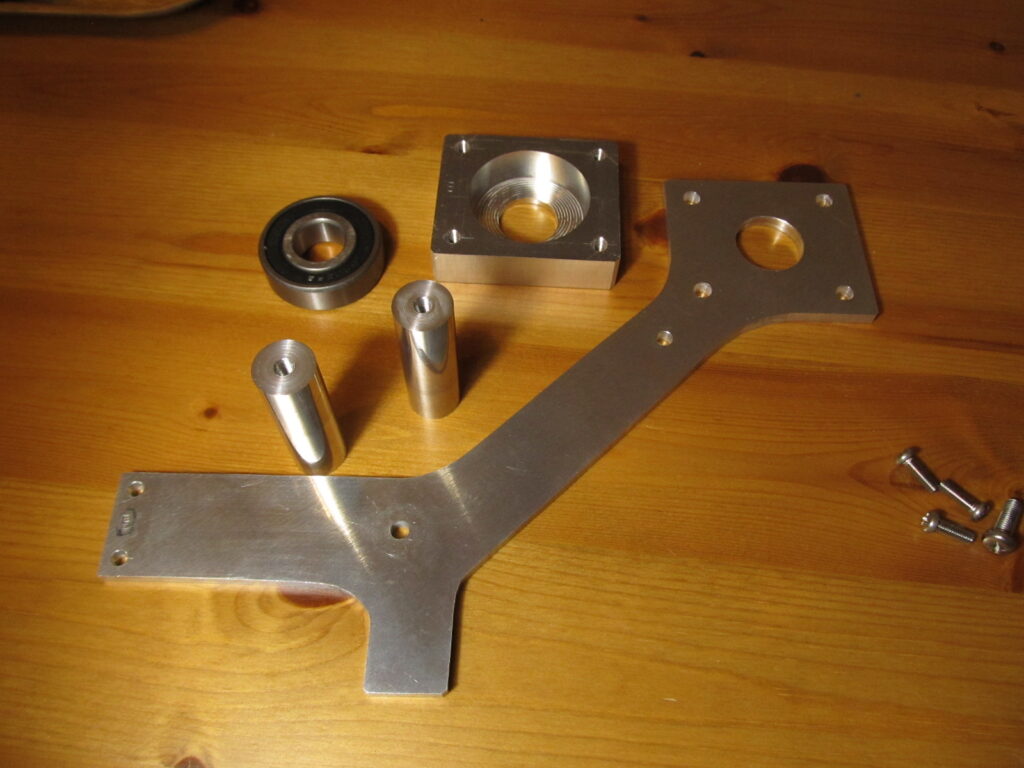
↓ベアリングをホルダーへ装着
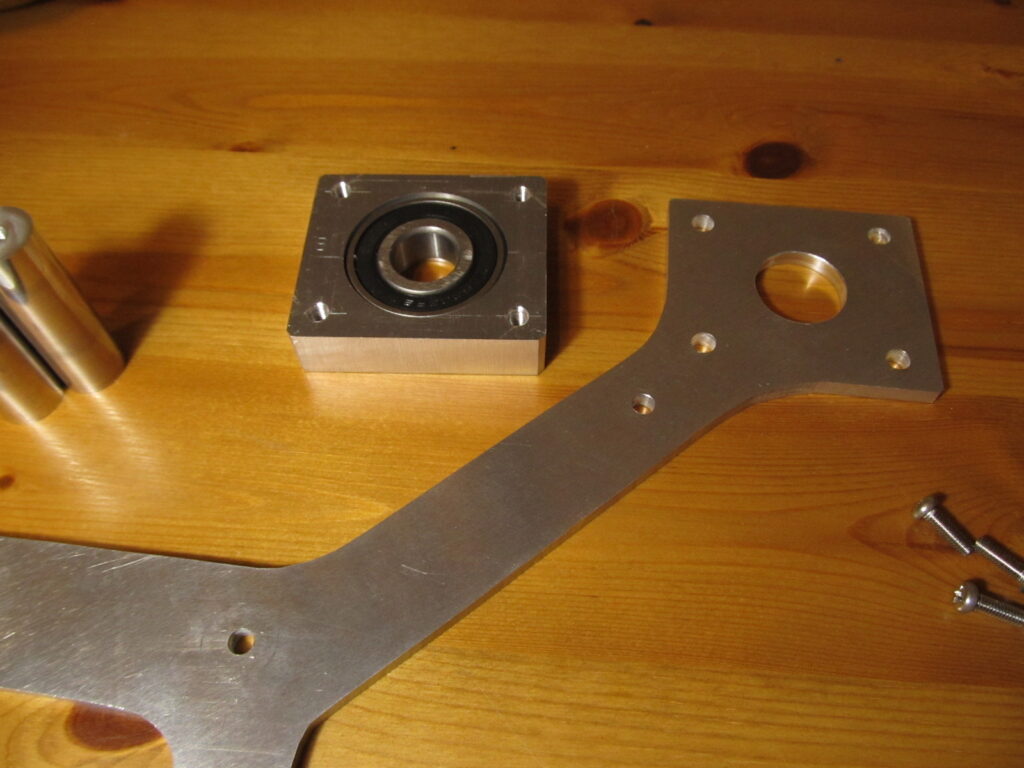
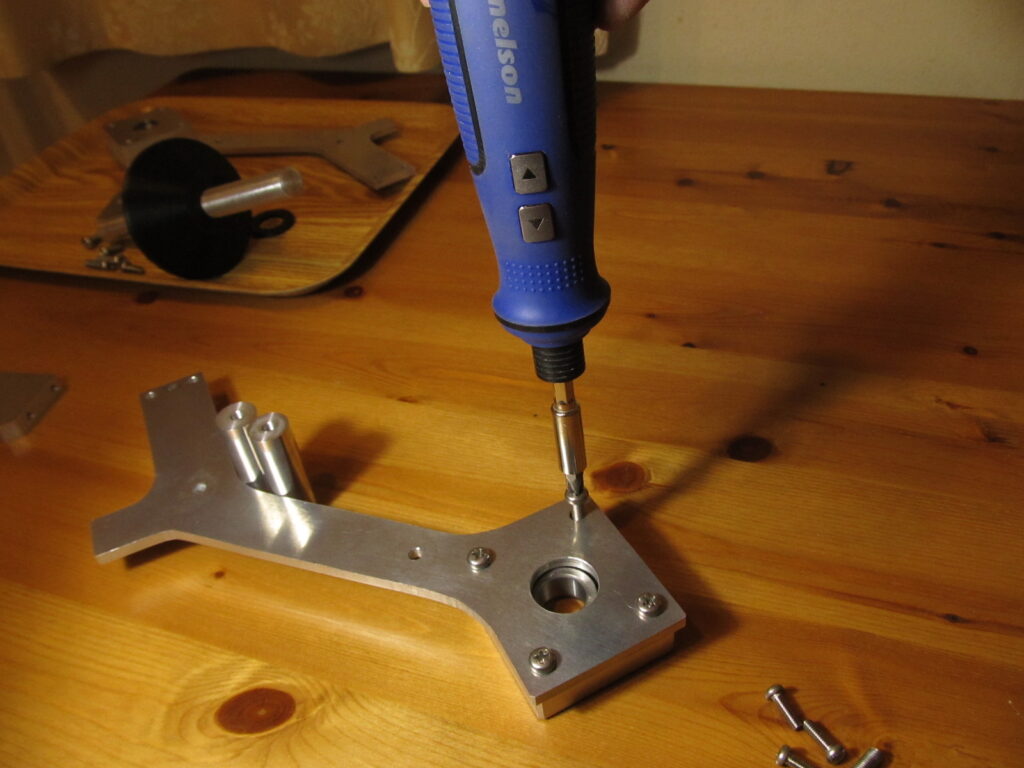
↓左右フレームの固定。Φ16㎜のアルミ丸棒で連結しています。
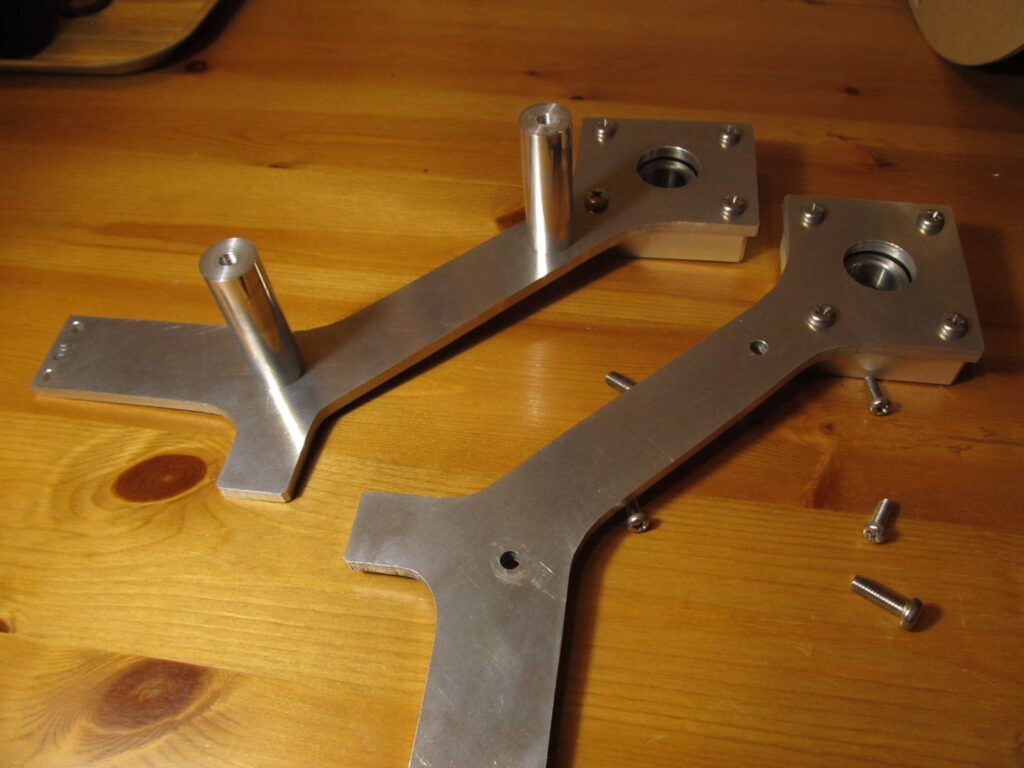
↓左右に幅を持たせ剛性を確保するというシンプルな構造です。
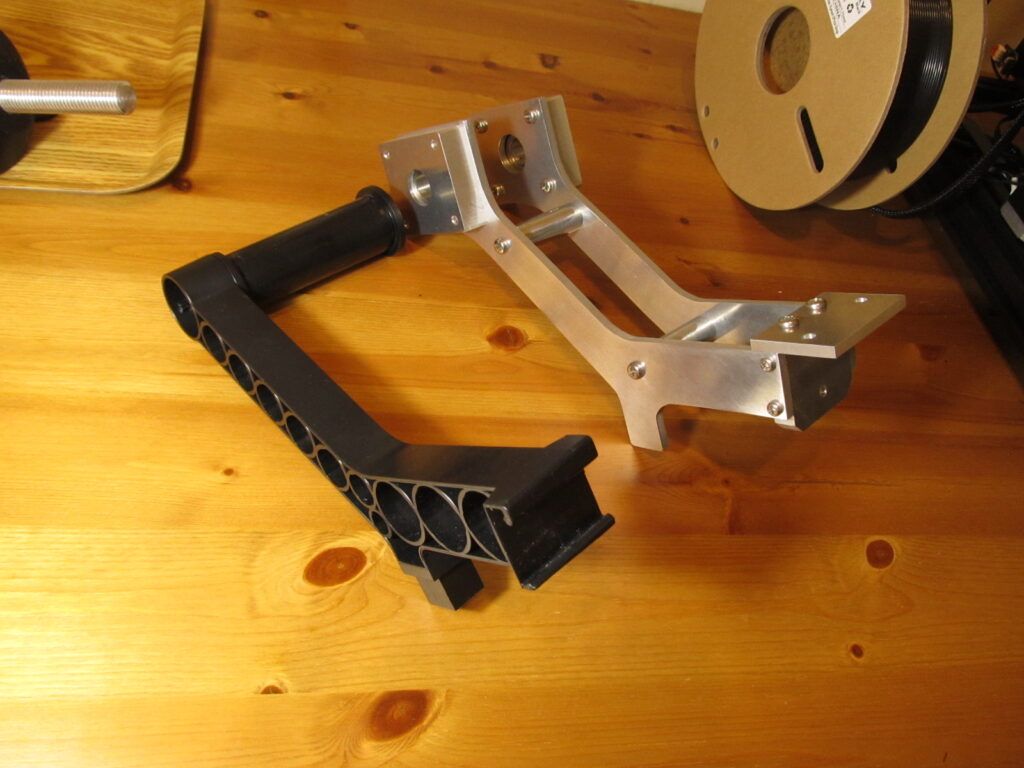
ちなみに黒いのが純正フィラメントホルダーです。1kgのフィラメントでゆらゆらしてしまいます。
3Dプリンタ本体への固定
3Dプリンタフレームへの固定はこのネジを使用。
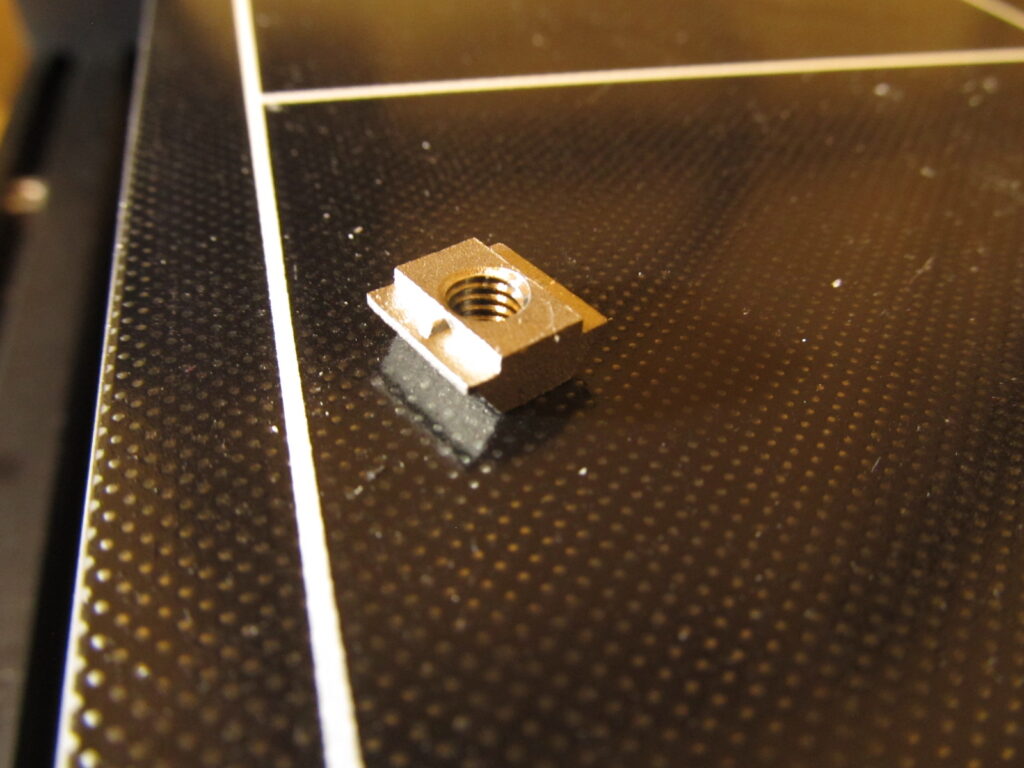
以前購入した、SUS(エスユウエス) STナット SS(M5) SFN-TX5 50個入のあまりです。
このプリンターに使用されているフレームは、SUSアルミフレーム、4040アルミフレーム(40㎜×40㎜)などと検索するとすぐ出てくる世界共通?品。
中国製機械のフレームといえばこのフレームです。 このアルミフレーム専用ネジです。
フィラメントホルダー完成
フィラメントを固定するとこんな感じ。
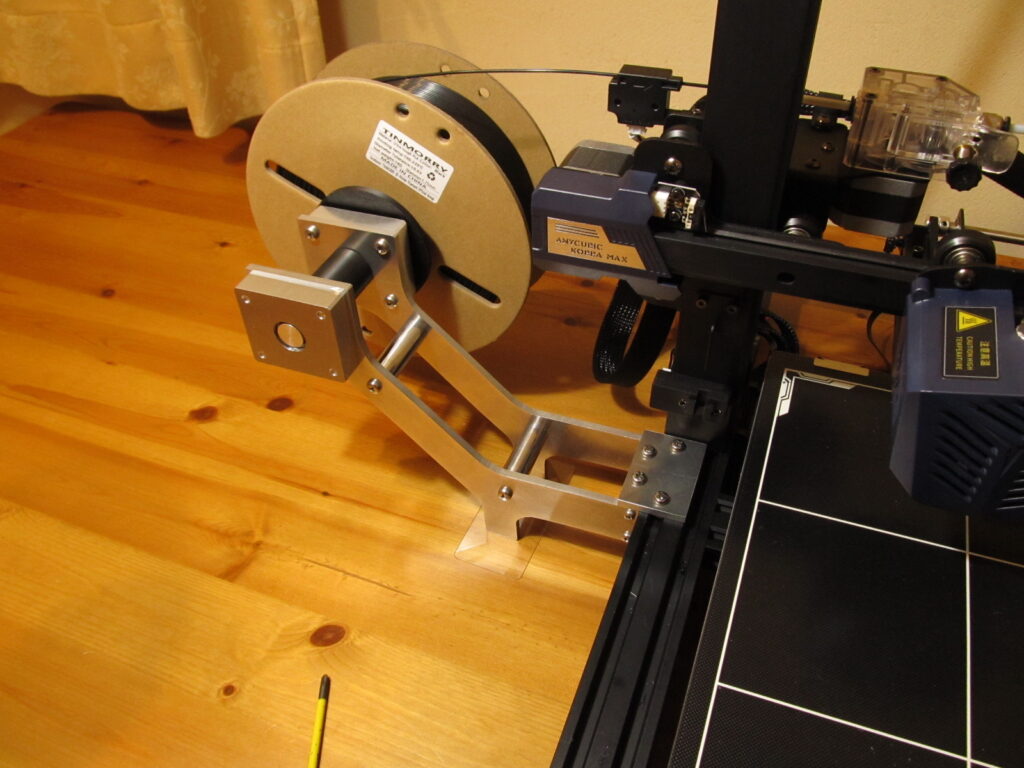
フィラメント固定ボルト(手回し用)もスムース回転しスピーディに固定できます。
スプール穴の直径が違ってもきっちり固定してくれます。
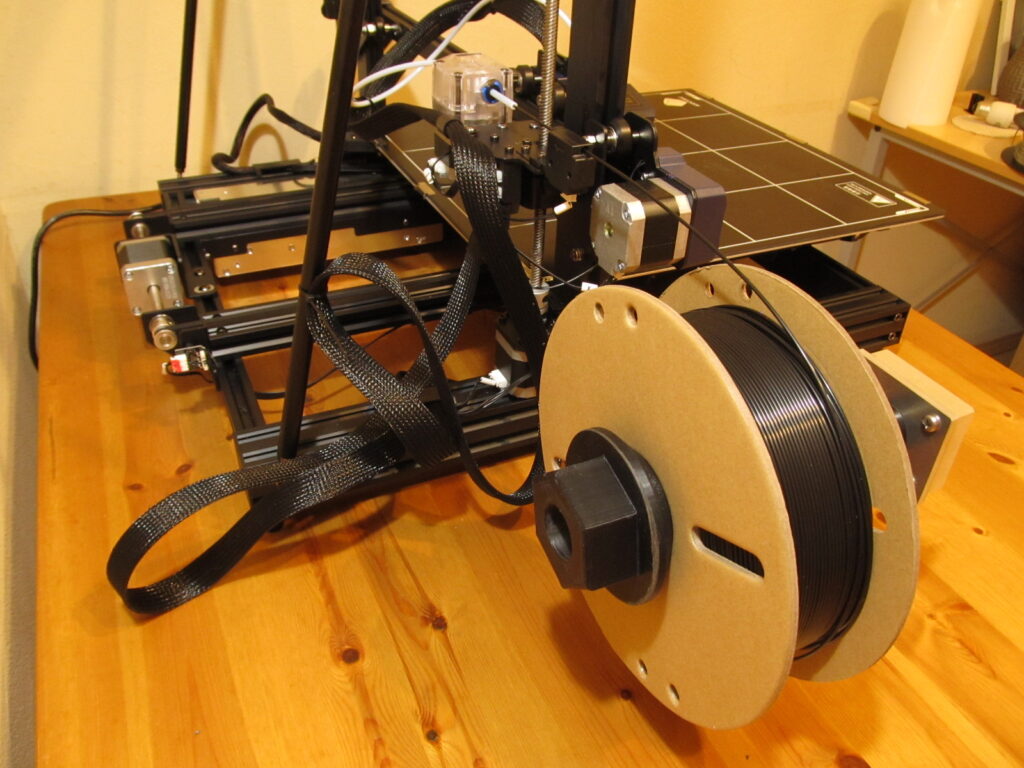
フレーム剛性バッチリです。ベアリング仕様なので回転も滑らかです。
文句のつけようがありません。
まだ使用していないのでいろいろ欠点が出てくると思いますが、それはそれで修正作業を楽しみましょう。
フニャフニャの樹脂アームからグレードアップできました!
ちょっとやりすぎ感がありますが、この不要な過剰品質がいいんです。