TIG溶接機を使うようになり、時々アルミも溶接するようになりました。
一つ道具を使えるようになると、何か作ってみたくなるものです。
長靴を買った子供が水たまりに入りたがるのと同じかな?
そこで、自作CNCフライス盤の切削液タンクをアルミ製にグレードアップしてみることに。
これです。ただの四角いアルミの箱。
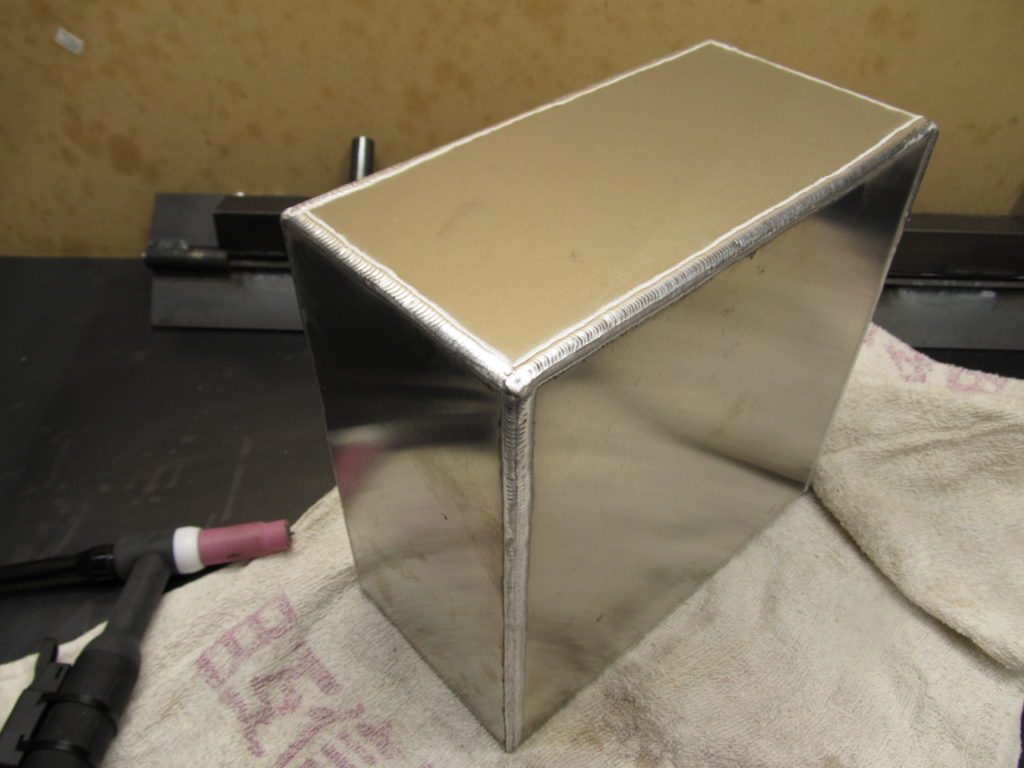
牛乳タンクと呼んでいます。水溶性切削油を使ったことのある方ならよくわかると思います。
水溶性切削油って水に混ぜると牛乳と同じ質感になるんですよね。ホント、コップに入っていたら間違えて飲んでしまいそうなくらいです。
以前は4リットルのオイル缶を流用していましたが、どうも見栄えが悪いなあと気になっていたので交換です。。
オイル缶なので切削液のタンクという目的は十分果たされているのですが、空き缶で出来ていると寄せ集めの装置のようでテンション下がります。
この空き缶がアルミ製タンクになると「お!アルミ溶接で作られているな!」と機能は同じでも・・・すてきな装置に見えてきます。
(自動車が)鉄チンホールでもアルミホイールでも「走り」に関してはあまり意味がないけど、「アルミがいい」、と同じですね。
DIYER共通の自己満足です。これが幸せにつながります。眺めてはニヤッ、です。
使用材料
アルミA5052、3㎜厚、ニップル作成用アルミ丸棒Φ25㎜、Amazonで売っている12Vポンプ。
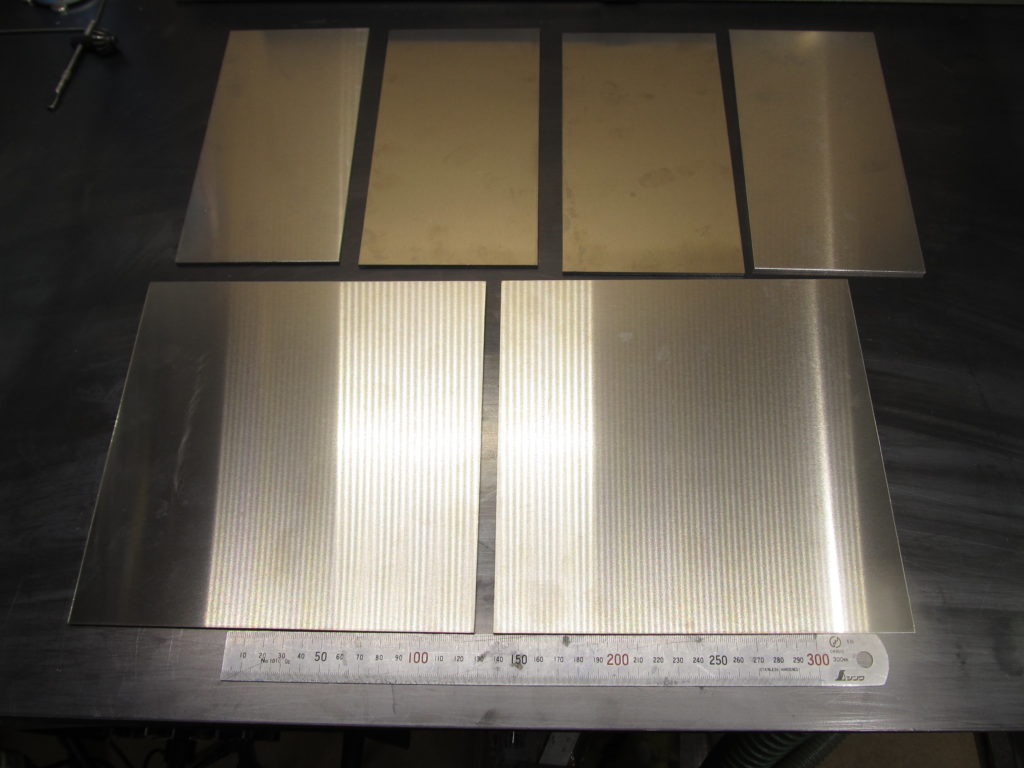
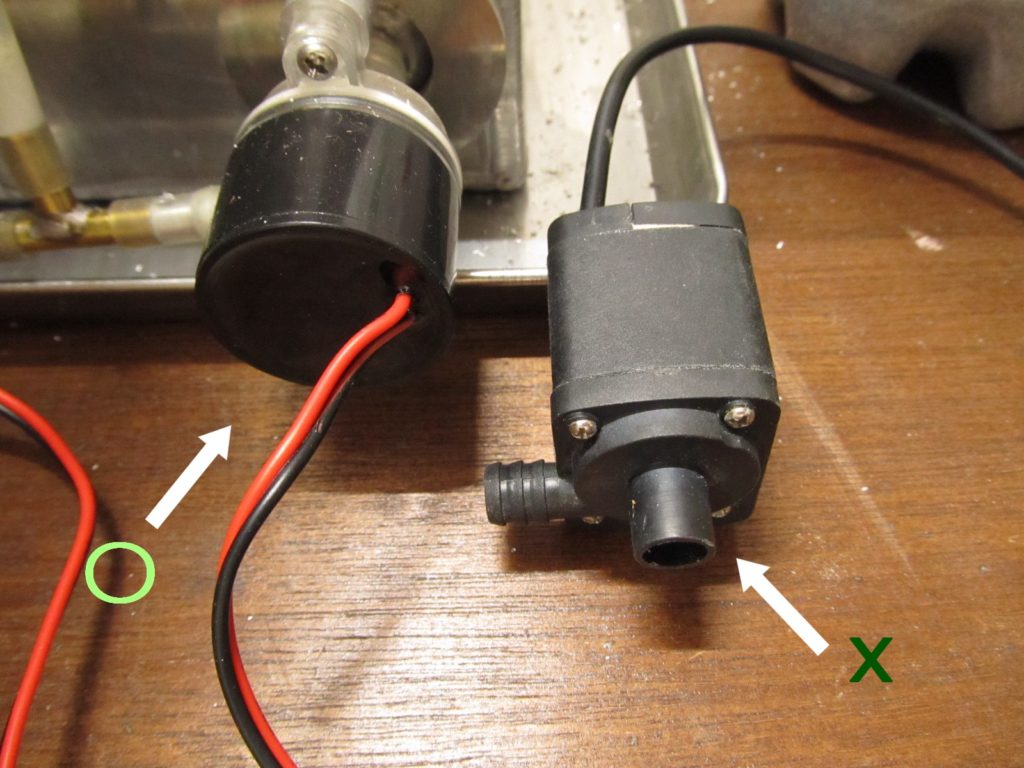
写真の右の四角いポンプは避けた方がいいです。
同じような規格、価格で一番入手しやすいタイプですが、水性切削液に使用していたら半年ほどで樹脂が侵食され漏水が始まりました。
探すのが大変ですが、丸い形状のアクリルっぽい樹脂製ポンプが安心です。1年はもっています。
作成過程
アルミ板のカットは自作パネルソーで行いました。
金属用パネルソー
このパネルソーは余った材料を活用しようと半分実験的な意味で作ったのですがかなり役立っています。後々グレードアップ版を作ろうと思うくらいです。
さて、切り出しサイズは次のように各辺が重なる大きさにします。なめ付けで溶接するためです。
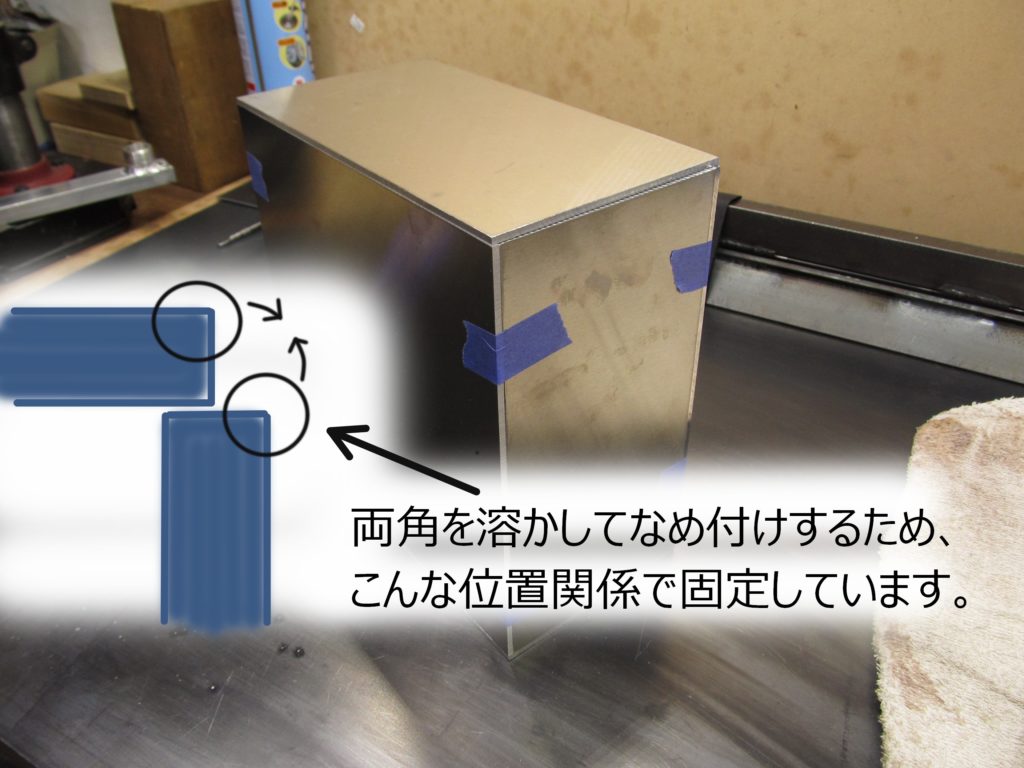
マスキングテープで仮固定し、点付けで溶接して様子を見てみます。
※点付け溶接機設定・・・溶接電流100A、タングステンΦ2.4㎜、パルス無し
仮付け後、大きな隙間が空いていないか、アルミ板が反っていないか、全辺確認し本溶接に入ります。
※なめ付け溶接機設定
溶接電流90A タングステンΦ2.4㎜、パルスON、
パルスFrequencyダイヤルは2時の位置、
パルスWidthダイヤル位置は3時の位置、
AC Balanceは20(最低位置)
溶接のコツ
といってもあまり経験がない初心者レベルの私が気を付けているところ・・・
①タングステンの位置
母材から3㎜程度 近いほどアークが飛び散らず、ピンポイントで加熱できる。
今回は、なめ付けのみで溶加棒を使わないので可能な限り近くしていますが、溶加棒を入れる時はもう少し離します。
溶加棒が溶けると、母材とタングステン間のアークにサッと吸い寄せられ盛り上がり、溶けたアルミがタングステンに引っ付いてしまいます。
はい、溶接中止→タングステン研磨、となります。(凹みます・・・)
②タングステンはいつもきれいに!
間違って溶けたアルミが付着したらすぐ中止して研磨します。面倒がってそのまま続けると汚い溶接になってしまいます。
③母材も溶加棒もきれいに脱脂
アセトンがよく使われているようです。面倒なのでパーツクリーナーで済ませています。
④トーチを持つ手に力を入れない
タングステンと母材の距離を一定に保ちながらトーチを動かす、となると緊張して力が入ってしまいます。
力が入るとプルプル・・・とぎこちない動きになり滑らかに動かせません。ハンドリューターなどの切削工具と違い、母材とトーチは何も接触していないので力は全く要りません。
⑤本溶接は点付けしたところから始める
2枚の板を点付けて橋渡していることでアークの熱が両母材に伝わり同時に溶け始めます。橋渡しされていないところだと、片側にアークが偏り溶接できません。
⑥始めゆっくり後半は速く
アルミは熱伝導が早いためアーク付近からどんどん熱が周りに伝播していきナカナカ母材が温まりません。
が、ある程度熱くなると溶解温度が低いためアッという間に溶け落ちが始まります。
そのためはじめはゆっくりですが、母材が熱くなってくる後半はサーっとトーチを移動させます。
以上を頭に入れながら・・・全辺を一回なめ付けし、溶け込みを確認して・・・もう一度なめ付けを繰り返し完成です!
アルミ溶接ってバイクのパーツっぽくてワクワクします!
一応、水をいれて漏れを確認しておきました。高圧タンクではありませんので漏れてこなければOKとします。
タンク内に水道パーツを流用したフィルターを設置してあります。
Φ10㎜ドリルでたくさん穴あけしたパイプに換気扇用不織布を巻き付けたフィルターです。
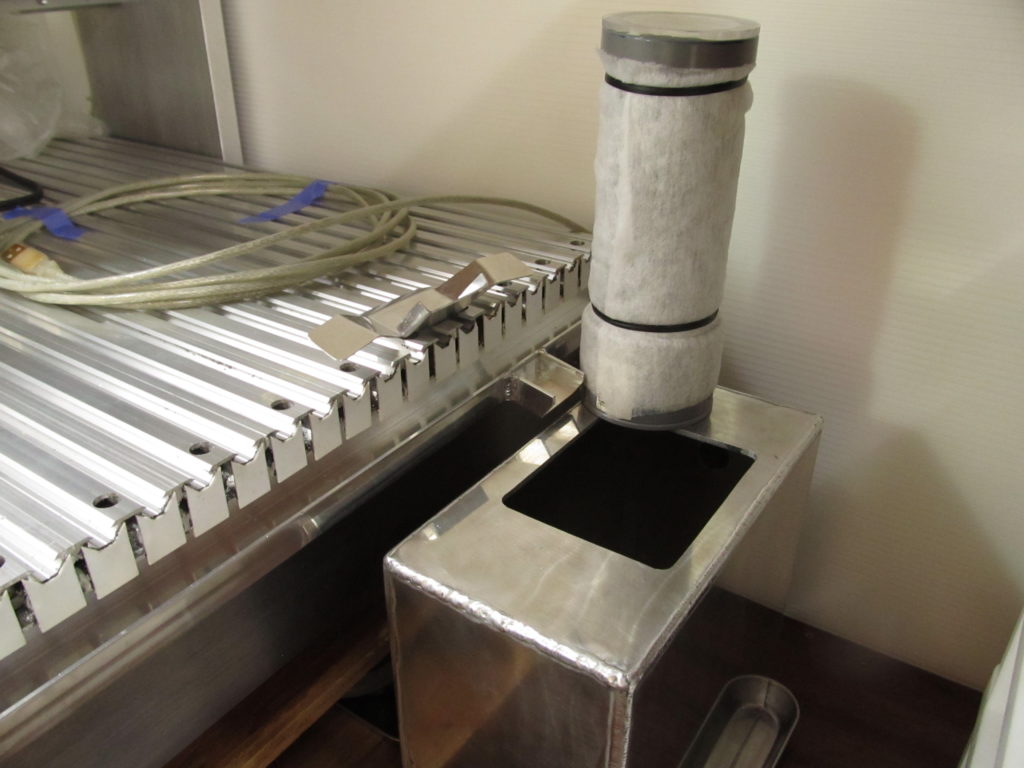
切削液循環装置の流れ
装置といってもシンプルにタンクから切削液がポンプで送り出されているだけです。
切削液は写真の緑色で表したとおりに循環します。
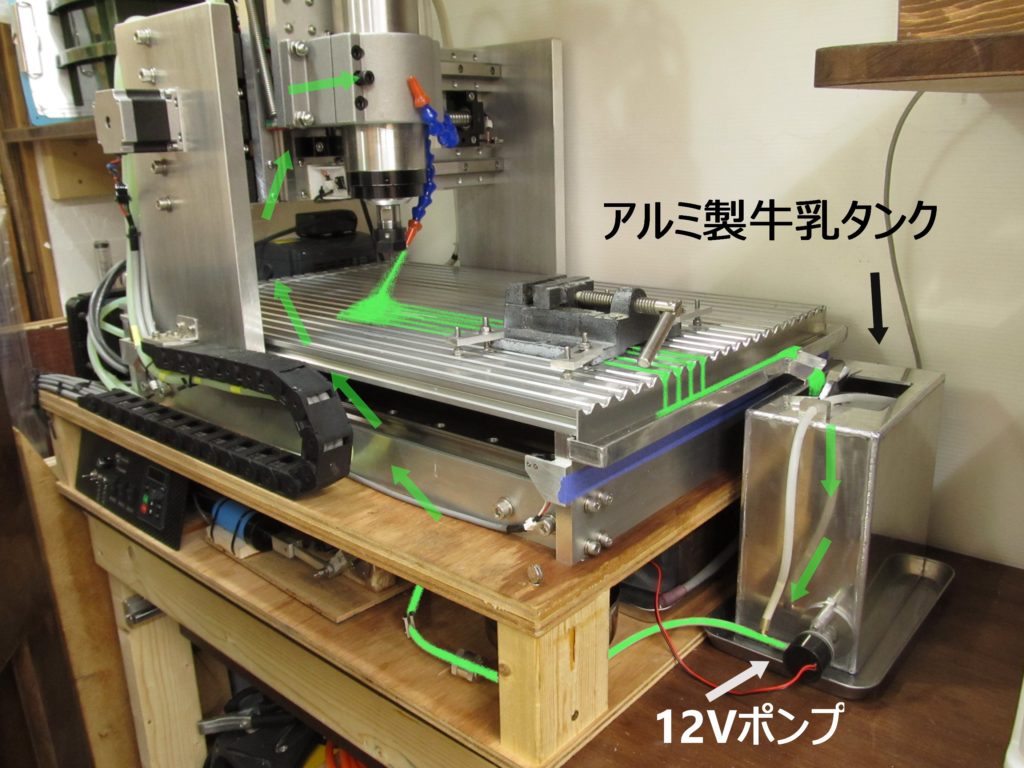
フライス盤テーブルから雨どいを伝ってタンクに戻るという単純なものですが、雨どいだけを伝って戻る形状がポイントです。
当初、雨どい部分からΦ8㎜程度のシリコンパイプでタンクに戻していましたが、途中で切削屑が蓄積して詰まることがありました。
CNCなので切削開始したら後はお任せ!と席を離れるのですが・・・、戻ってくるとパイプが詰まり切削液が溢れかえっていることがありました。泣~
パイプは、曲がりがあると緩やかに見えても切削屑の大きさ形状によって詰まることがあります。
一度詰まりを経験すると心配で切削中フライス盤から離れられなくなります。
そのため、詰まることのないオープンな雨どい形式に行きつきました。
今後の課題
せっかくTIG溶接でカッコイイアルミタンクができたのですが、実際使ってみるとまだまだ改善が必要でした。
〇フィルターはコーヒーのろ紙のように目の細かいものに変更が必要。
切削屑は大き目と粗目のフィルターにしましたが結構通過してしまいます。
〇ポンプ~噴射ノズルまで距離が1m強あるのでポンプONから噴射までタイムラグが長い。
〇多量の切削屑を完了後に手動で集めるのはローテク感がある。切削屑もすべて自動で回収する方法はないか。
切削後、サッときれいな部品だけ取り出せるとカッコイイのになあ。
いつまでも工作の課題が尽きません。仕事に行っている場合じゃない!