今回の作業記録はCNCフライス盤用の集塵カバーでございます。
集塵カバーは、木材・MDFボード、樹脂などの切削時に粉塵が舞う材料を切削するときに使うモノ。
CNCフライスの使用はアルミ切削が主で木工などの粉塵対策はしていなかったのですが、最近購入しましたレーザーカッターに触発されCNCフライスも気楽に使えるように整備してやりたくなりました。
レーザーでの木製品への刻印テスト中「レーザーは早い・簡単だけど、立体的に彫れるフライス盤での切削もいいなあ」なんて思い始めたんです。
レーザーカッターが得意とする加工、フライス盤が得意とする加工がありますので両方ともすぐに使えるようにスタンバイしておきます!
早速、集塵カバーの作製です。
カバー無し状態のフライス盤
現状はこのように2本のノズルが構えております。

アルミ切削用のクーラントノズルとスレートなどの石材切削用の水ノズルです。
一応市販の集塵カバーはないかなと検索したのですが、私のフライス盤にフィットする集塵カバーはなさそうです。
スピンドルモーターの直径が52㎜や65㎜の小径のモノはありました。
出来れば市販の透明タイプが欲しかったのですが、売っていないので自作するしかありません。
今回は3Dプリンターに活躍していただきます。 透明パーツは作れませんが、円筒形や箱型といった丸や四角の組わせのパーツは3Dプリンターだと簡単です。
3Dプリンターで出力したパーツです。
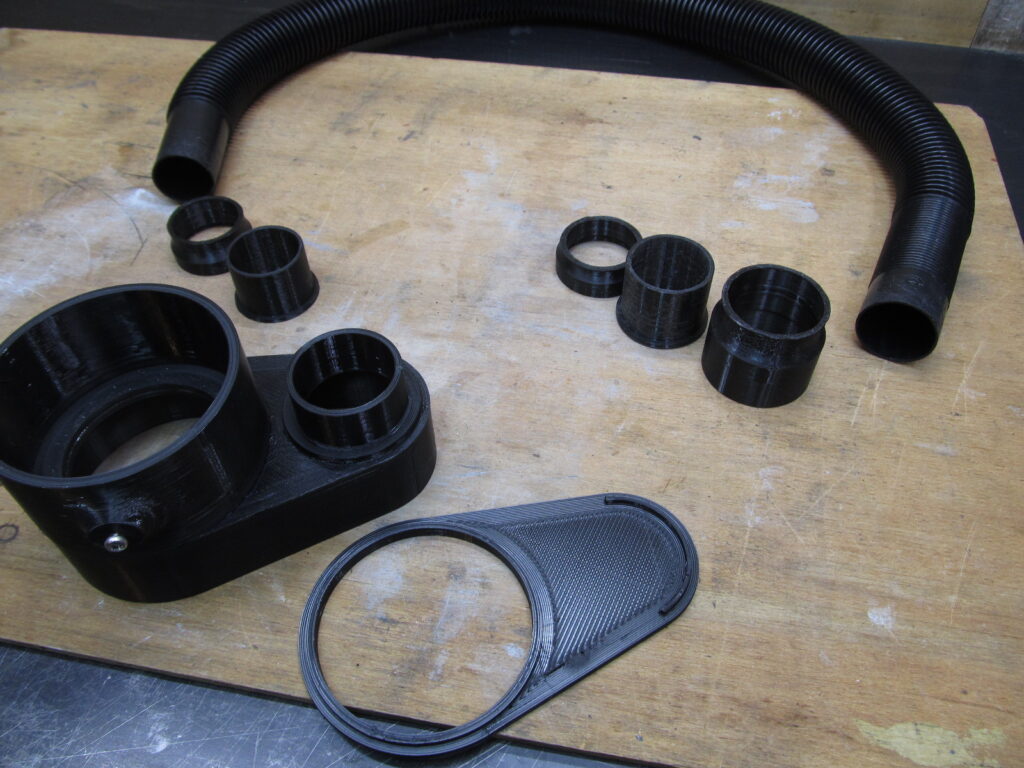
これらを組わせていきます。
3Dデータ作製は少々ハードルが高いのですがプリントした後の作業はとても楽。
黒いホースの両端が単なる差し込み口ではなくいくつかのパーツに分かれております。 これはのようにフリーに回転させるためです。
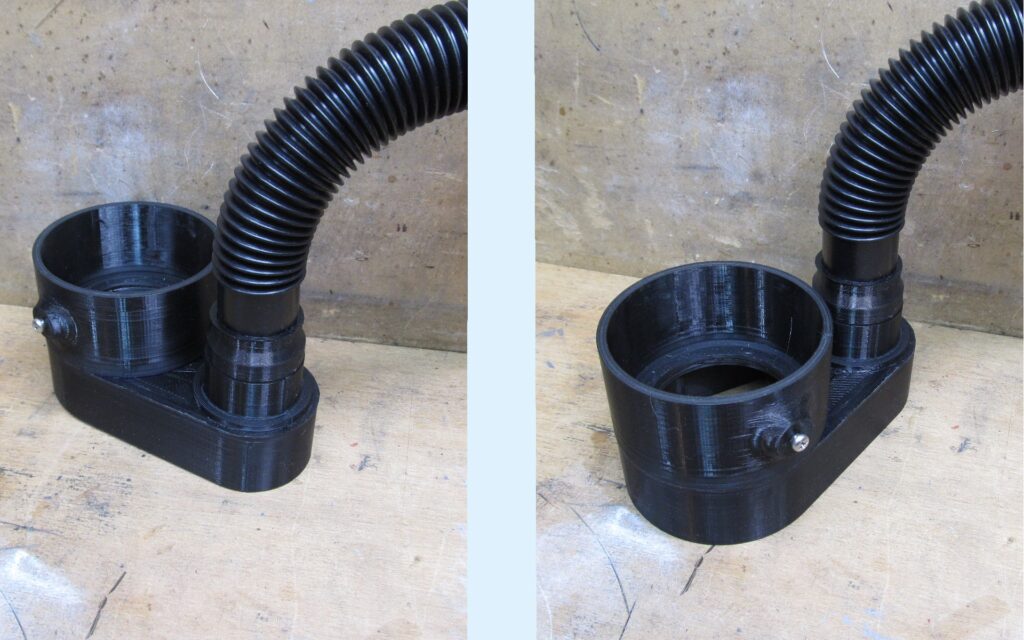
黒いホース(ボッシュのフレキシブルホース)は結構柔軟なのでフライス盤の動きに追従できないわけではありませんが、根本が回転できないとホースに「捻じれる力」がかかります。
ちょっと無理している感じですね。
やはり機械はスムースにストレスなく稼働してほしい・・・と 少々手間ですが回転軸を設けました。
写真では首振りは90°だけですが360°クルクル回ります。 内側のパーツと外側のパーツの直径差を0.4㎜程度にしてあるのでかなり滑らかに抵抗なく回ってくれます。
3Dプリンターの精度
手作業とは比較になりません。 手作りが好きな私としてはちょっと悔しいのですが、このような円筒形で摺動するパーツは3Dプリンターにお任せしております。
(強度が必要とか耐熱性が求められる場合はアルミ+旋盤で作ります)
うちの3Dプリンターは円筒形をプリントすると内径の直径が0.6㎜小さくなります。外径の直径は0.2㎜小さくなります。
このクセを覚えておきCADでデータを作ります。
今回のクルクル回るパーツは、
外側の筒(軸受けに相当)の内径は36.8㎜(CAD上)-0.6㎜ ⇒36.2㎜でプリントされました。
内側の筒(軸に相当)の外径は36.0㎜(CAD上)-0.2㎜ ⇒35.8㎜でプリントされました。
よって、外側の筒と内側の筒のサイズ差は0.4㎜となります。 これでスムースに回転してくれます。
このような微妙なサイズ差を実現してくれるので結構助かっています。
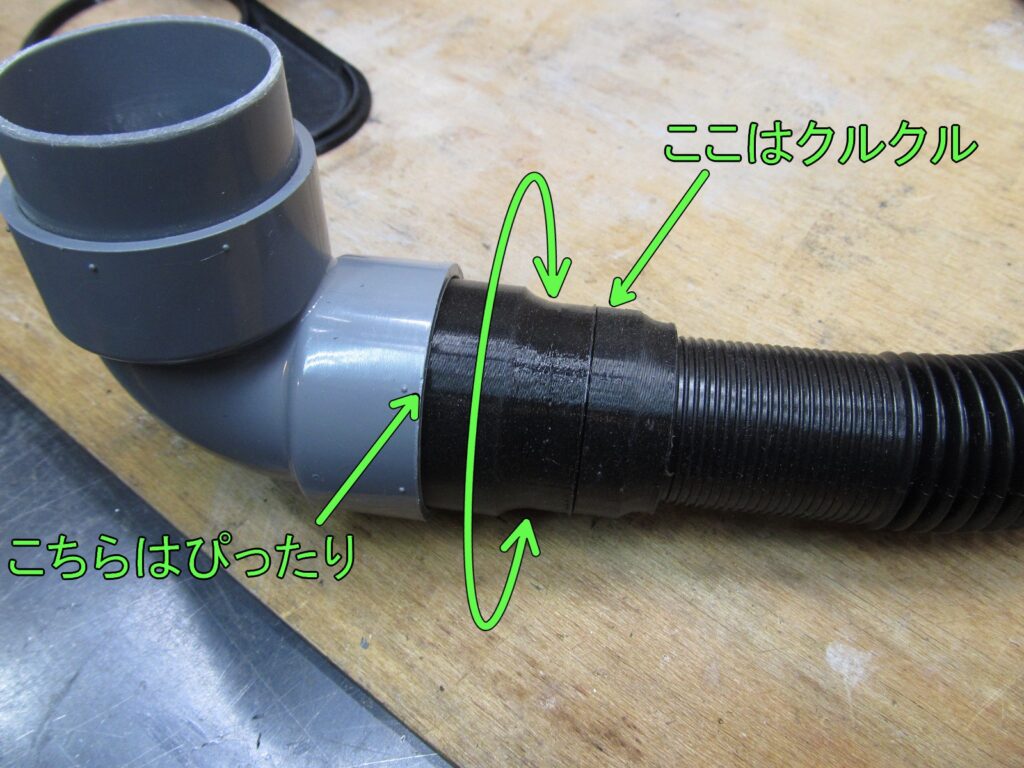
3Dプリンターの樹脂(フィラメント)
樹脂はPETGのみを使っています。
3Dプリンター購入当初はいろいろ試しました。樹脂の種類で言えばPLA、ABS、PETGの3種類。
同じ樹脂でも仕上がりががツルツルになるタイプ、マット仕上げになるタイプ、カーボン入りなどがありますのでいろいろ試してみました。
十数本試してみましたが、今の私の用途にはPETGがベストです。
ちょいと高めのメーカ品も試しましたが今はお手頃価格の「OVER TUREのPETGフィラメント黒」のみを使っています。
ブラシ部分は刷毛を移植
エンドミルの周囲をカバーするブラシ部分をどうするか?
市販の集塵カバーがすべてブラシ状なのでこれが最適解なのでしょう。真似するしかないと思いますが、問題は作り方・・・。
結局、ちまちまと植毛することになりました。 ↓ 植毛の様子です。

毛の弾力性がよいナイロン刷毛を分解して一束を爪楊枝くらいのサイズにほぐします。
UVレジンを黒リングに一滴付けてナイロン毛を置きます。
適度な位置に置けたら紫外線ランプを照射します。
これの繰り返しです。
ナイロン毛は軽いのでちょっと触れるとすぐ動いちゃう。適切な位置への配置がちょとイライラ。
一周植毛するのに2時間以上かかりました。
じーっと座っての作業、精神力が試されます。 修行している気分になりました。
ネオジム磁石(極小)で脱着式に
このブラシ付き黒リングはΦ3㎜のネオジム磁石で取り外し式にしました。
ネオジム磁石って直径2㎜とか棒状のモノとかいろいろ売っているんですね。 いろんなものが作れそうでワクワクしてきました。
Φ3㎜なのでドリルで穴を開けて瞬間接着を付けて押し込むだけ。 これを一周8か所に配置。
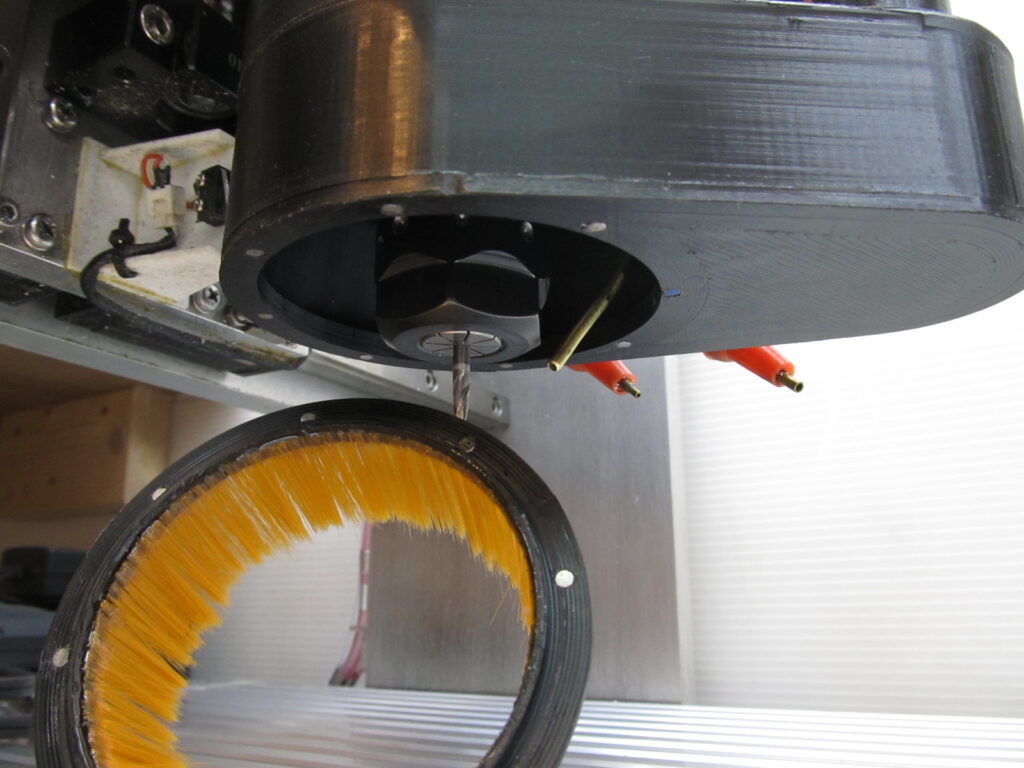
これでブラシがためになっても簡単に交換できます。
斜めに出ている細い真鍮パイプはエアダスター?です。 レーザーカッターに使うエアアシストポンプに接続して切削屑を飛ばすためのノズルです。
「切削屑をエンドミルが巻き込まないため」&「木屑を舞い上がらせて集塵しやすくする」という効果があると思っております。
完成
全体はこんな感じでございます。
木工する時はこの状態で切削し、アルミ切削時は黒いパーツはすべて取り外します。
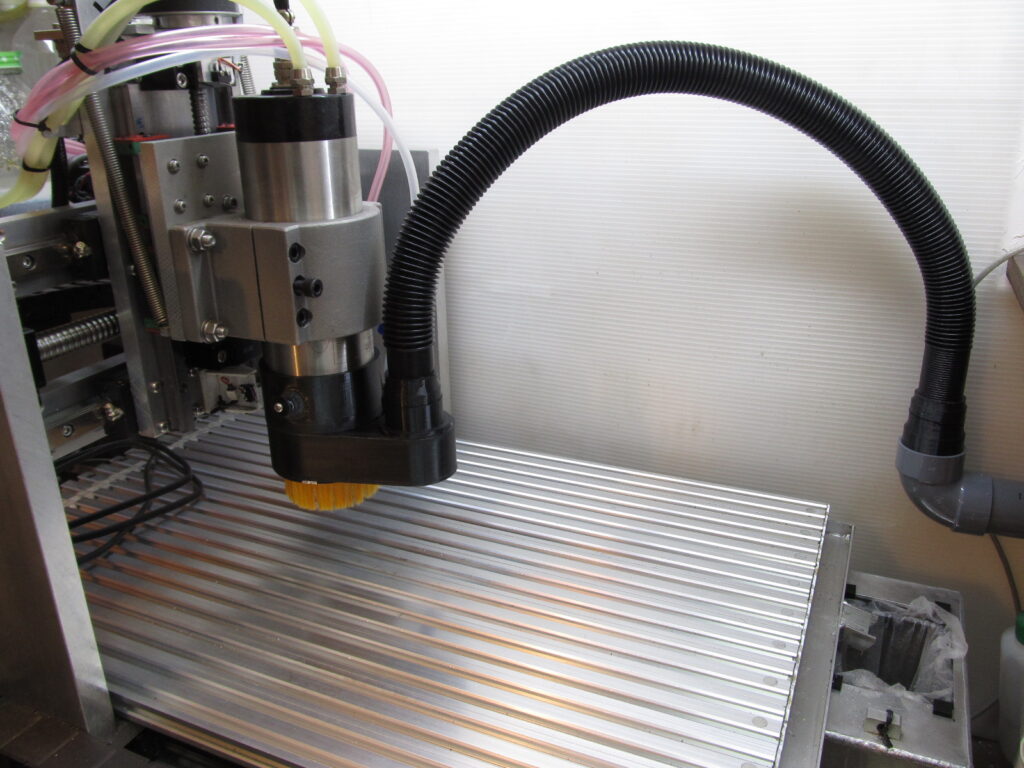
黒いホースの右側、塩ビ管はΦ40㎜の排水管用パイプです。
これは天井の集塵機につながっておりフライス盤稼働時は集塵機をオン状態にします。 手動です。連動はしていません。
エア供給チューブはこちら側。
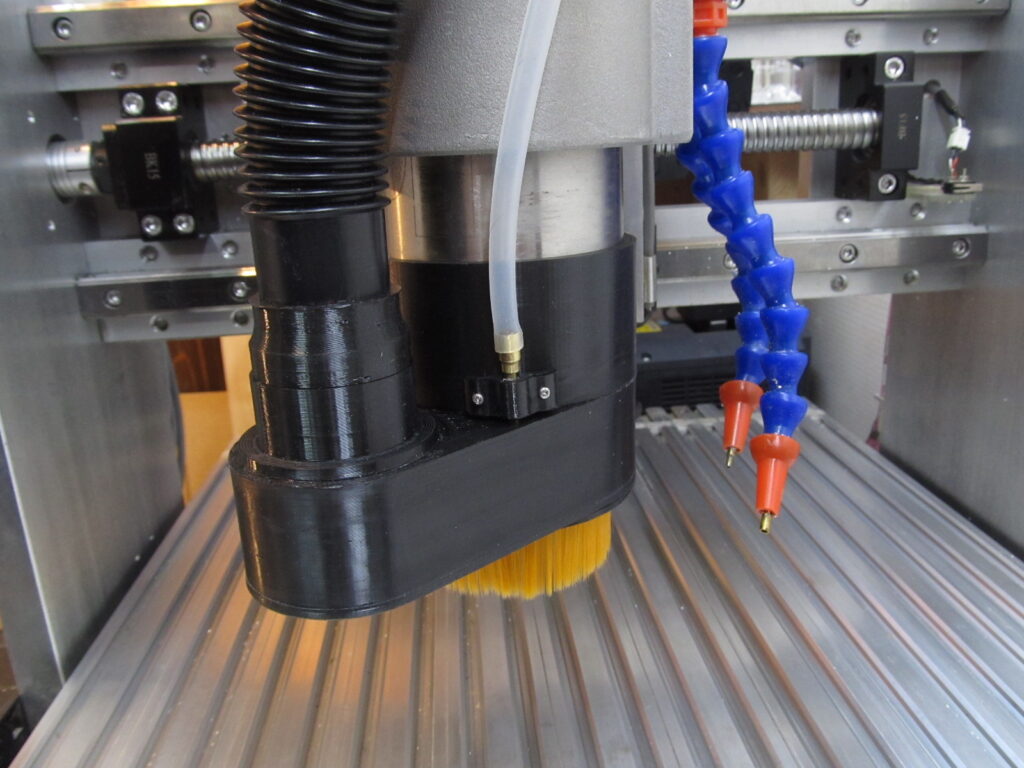
この真鍮パイプを固定する留め具(2本のネジでとまっている)も3Dプリンターで出力すると円筒部分にピッタリサイズで作れます。 当たり前だけど感動します!
これで木工対策万全です! 粉塵の舞う木工が気楽に出来るようになりました。
いつでも木工のご依頼、ウェルカムという気分です。(笑)
あくまでも気楽に加工できるぞ~という気分でして、加工の請負などはしておりませんよ。